Eingerahmt
Die Bezeichnung "Rahmen" trifft bei den konventionellen Motorrad-Fahrwerken den Nagel auf den Kopf. Schließlich spannten sich die klassischen Doppelschleifenrahmen in ausladender Form um den kompletten Motor, der nahezu frei von allen Biegekräften blieb, die sich an einem Motorrad aufbauen. Entsprechend leicht und filigran konnten Motorgehäuse und Zylinderblock konstruiert werden. Zudem erlaubte dieses Rahmenkonzept eine elastische Lagerung des Motors, um der Vibrationen Herr zu werden.
Die ursprüngliche und logische Idee, den Lenkkopf auf direktem und kürzestem Weg mit der Schwingenlagerung zu verbinden, blieb jedoch beim konventionellen Doppelschleifenrahmen auf der Strecke.
Dabei zeigten einige berühmte Maschinen wie die NSU Max (Blechprofil-Brückenrahmen) oder die seltene Horex RS 350 von 1954 (Brückenrahmen aus Dreiecks-verbänden), dass die Einbindung des Motors als tragendes Element eine hohe Stabilität bei extrem wenig Gewicht garantiert, wenn das Motorgehäuse den Belastungen entsprechend geformt war.
Mitte der 80er-Jahre rollten wieder Motorräder vom Band, die den Rahmen-/Motorverbund nutzen. Hondas VFR 750 F von 1986 trug das erste Rahmenkorsett aus Aluminiumprofilen, die Konkurrenz rückte nach, und Yamaha legte mit der FZR 1000 Genesis mit Aluminium-Deltabox-Rahmen noch einen drauf. Bei genauer Analyse der bildschönen Deltabox-Konstruktion wurde jedoch klar, dass die Funktion nur deshalb sichergestellt war, weil die verschraubten Unterzüge, die den Motor in elastischen Gummilagerungen aufnahmen, das Gebilde stabilisierten.
Erst als man die Motorgehäuse starr in den Aluminium-Rahmen verschraubte (Honda VFR 750 F/R, Yamaha FZR 750R etc.), war die Verwindungssteifigkeit der Verbundkonstruktion optimal genutzt.
Um Kosten zu sparen, wurden im Laufe der Zeit die aufwändig verschweißten Konstruktionen aus glänzenden Formblechen (Yamaha YZF R1 von 1998) oder eleganten Strangpressprofilen durch kostengünstige Gussteile ersetzt. Obwohl sich manche dieser Brückenrahmen in filigraner Form über den Motor spannen, entsteht durch das verschraubte Motorgehäuse ein großer umbauter Raum, der die Biegekräfte und -momente bestens im Griff hat.
Dasselbe Prinzip, jedoch mit einem technisch wie optisch völlig anderen Lösungsansatz, verfolgt Ducati. Statt Aluminiumguss verwenden die Italiener in Dreiecksverbänden angelegte Stahlrohre, die leicht und extrem stabil den Motor inte-grieren. Zudem nutzt Ducati das eigenständige Rahmenlayout als markantes Design-Element. Rot lackiert und sichtbar zur Schau getragen, hebt sich der Ducati-Rahmen nachhaltig von der japanischen Massenware ab.
Auch aus Stahl, aber in Form und Ausführung deutlich simpler, sorgen so genannte Einrohrrahmen bei Enduros oder kostengünstigen Mittelklassemaschinen für ausreichend hohe Stabilität bei minimalen Kosten.
Doch egal, ob Stahlrohr- oder Aluminiumrahmen, an alle Konstruktionen stellen sich große mechanische Anforderungen. So muss eine gewisse Biege- und Torsionssteifigkeit gewährleistet sein, um die Räder auch bei hohen Belastungen ohne Verschränkung in der Spur zu halten. Wird die Steifigkeit jedoch zu hoch angesetzt, leiden der Fahrkomfort und die Rückmeldung an den Fahrer. Das heißt, der Rahmen sollte im Lenkkopfbereich in vertikaler Richtung, also bei kurzen harten Stößen, mit einer bestimmten Flexibilität die Federung unterstützen, ohne sich bei harten Bremsmanövern zu verwinden. Aufgaben, die sich zwar durch Computerberechnungen grob entwerfen, aber nur in echten Fahrtests tatsächlich nachweisen lassen.
Diesen Mix aus der nötigen Steifigkeit und gezielter Flexibilität erreichen die Konstrukteure durch den Einsatz unterschiedlich dicker Wandungen und Profilquerschnitte. Wie komplex und zum Teil widersprüchlich dieser Fahrwerks-Hokuspokus sein kann, demonstrieren die Teams in der MotoGP. Dort werden von einem zum anderen Rennen Rahmen verstärkt, dann wieder abgeschwächt, um zwei Rennen später mit noch mehr Materialauftrag oder Bauteilen aus Karbon noch mehr Steifigkeit zu besitzen.
Welche brutalen Kräfte an einem Motorradrahmen ansetzen, lässt sich anhand einer Vollbremsung mit Sozius oder beim vollen Einfedern einer rund 400 Kilogramm schweren Tourenmaschine anschaulich demonstrieren. Diese Kräfte und Momente im Tonnenbereich entstehen durch die Hebelwirkung der Gabel beziehungsweise der mechanischen Übersetzung der Federkräfte an der Schwinge. Im Rahmenbereich zwischen Schwingenlager und oberem Federbeinauge treten beim Überfahren von Bodenwellen Kräfte bis zu tausend Kilogramm auf. Und genau hierin liegt die wohl heikelste Aufgabe im Rahmenbau. Tausende von Kraftspitzen muss der Rahmen über die Jahre aushalten, ohne zu ermüden und letztlich zu zerbrechen. Was beim Ruf nach sportlichem Leichtbau einer Gratwanderung mit verbundenen Augen gleichkommt.
Doppelschleifenrahmen
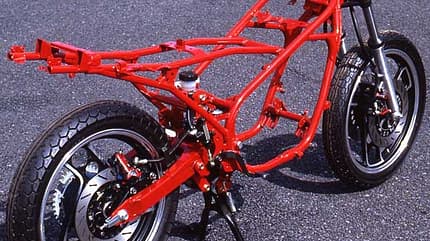
Bei der Yamaha RD 350 YPVS aus den 80er-Jahren setzten die Konstrukteure auf das klassische Rahmenkonzept der legendären TZ-Baureihe, jedoch mit vergleichsweise dünnen Stahlrohren. Auch wenn der Lenkkopfbereich mit einigen Knotenblechen verstärkt wurde, war dies die Schwachstelle der Yamaha und sorgte mitunter für immense Probleme in der Fahrstabilität. Um die Vibrationen des 350er-Zweizylinder-Zweitaktmotors zu zügeln, wurde er an den vorderen Aufnahmen in elastischen Gummielementen verschraubt.
Einrohrrahmen
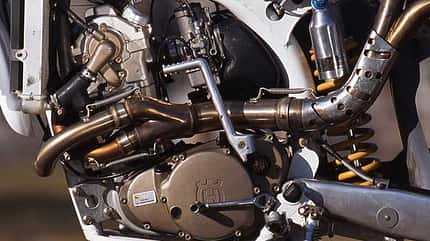
Bei diesem simplen Rahmenkonzept zieht sich ein armdickes Stahlrohr vom Lenkkopf bis zum Schwingenlager. Meist bei Enduros und Motocross-Maschinen verbaut, genügte die Stabilität, um die relativ geringe Motorleistung von rund 50 PS zu bändigen. In Verbindung mit einer geteilten unteren Rahmenschleife, den sogenannten Unterzügen, hat sich dieses Bauprinzip bis heute auch bei kostenkünstigen Straßenmaschinen
etabliert.
Brückenrahmen mit Unterzügen
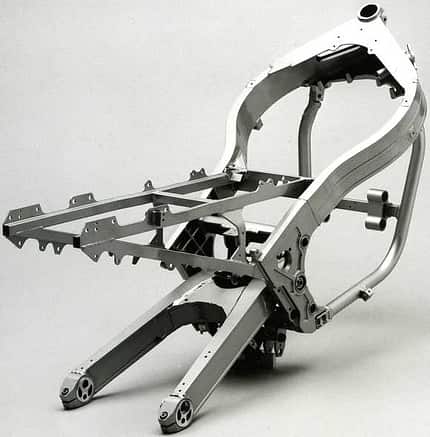
Mitte der 80er-Jahre wurden die ersten Alu-Brückenrahmen mit angeschweißtem Rahmenheck salonfähig, bei denen zwischen Lenkkopf und Schwingenlagerung stabile Aluminium-Strangpressprofile verschweißt waren. Doch anstatt den Motor als tragendes Element einzubinden, wurde dieser in wuchtigen, verschraubten Rohrunterzügen mit elastischen Lagerungen befestigt. Gut zu erkennen sind die massiven Gussteile im Schwingenlagerbereich, wo sich auch die hohen Kräfte des Zentralfedersystems abstützen.
Aluminium-Brückenrahmen
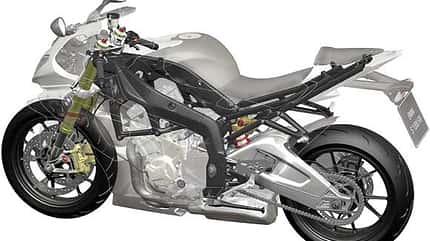
Auch BMW hält sich mit der neuen S 1000 RR streng an das japanische Rahmenkonzept. Aus verschiedenen Guss-Segmenten verschweißt, erhöht der Vierzylinder-Reihenmotor durch die starre Verschraubung an Zylinderkopf und im Schwingenlagerbereich den tatsächlich umbauten Raum und damit die Steifigkeit drastisch.
Gitterrohr-Brückenrahmen
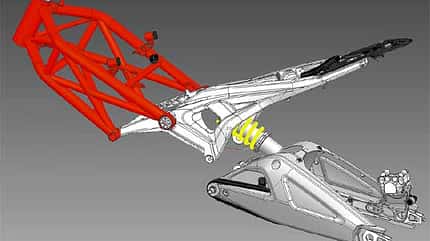
Ducati setzt seit den ersten V2-Motoren auf das Bauprinzip, das sich die enorme Steifigkeit von Dreicksverbänden zunutze macht. Das Ergebnis sind leichte und stabile Rohrrahmen, die im Fall der Monster mit dem verschraubten Stahlrohr-/Alugussverbund zudem für eine schicke Optik sorgen.
Stahlrohr-Brückenrahmen
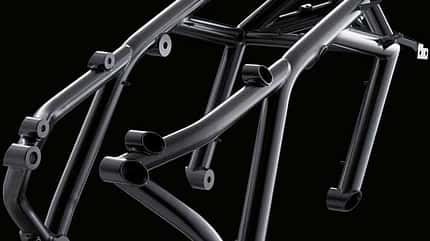
KTM verschraubt den großen V2-Motor der RC8 an sechs symmetrischen Punkten zu einem stabilen Verbund und verzichtet dabei auf jegliche eingeschweißten Querstreben im hinteren Rahmenbereich. Dank der nur 1,5 und 1,2 Millimeter dünnen Rohrwandungen geriet der Rahmen mit 7,2 Kilogramm (ohne Heckrahmen) fast drei Kilogramm leichter als die japanischen Alu-Konstruktionen.
Belastung bei Vollbremsung

Der Lenkkopfbereich ist beim Bremsen extremen Biegemomenten ausgesetzt. Bedingt durch die Hebelwirkung aus Vorderradhalbmesser und Gabellänge wird der untere Bereich nach hinten gestaucht, während der Rahmen am oberen Lenkkopflager gestreckt wird. Kräftige Querversteifungen unterbinden ein Aufweiten der Rahmenprofile.
Belastung am Lenkkopf oben: ca. 950 kg
Belastung am Lenkkopf unten: ca. 1200 kg
Belastung mit Zuladung
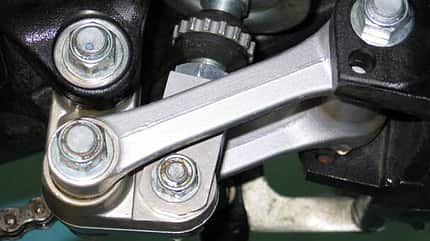
Bei maximalem Gesamtgewicht (rund 460 kg) liegen etwa 65 Prozent der Last auf dem Hinterbau des Rahmens. Bei tiefen Bodenwellen kann sich diese Last durch den dynamischen Einfedervorgang verdoppeln.