Zur Beatmung eines Viertaktmotors dienen die Ventile. Sie haben die Aufgabe, den Verbrennungsraum während des Kompressions- und Arbeitstakts gegen die Kanäle abzudichten und die Gaswege während des Ansaug- und Auspufftakts freizugeben. Über Einlaßventile gelangt zündfähiges Benzin-Luft-Gemisch in den Brennraum, über Auslaßventile werden die verbrannten Gase in den Auspuff entlassen. Die dabei auftretenden enormen thermischen Belastungen stellen hohe Anforderungen an die verwendeten Materialien.
In Viertakt-Motorradmotoren werden zwei, drei, vier oder fünf Ventile pro Brennraum eingesetzt. Die Einlaßventile, die bei jedem Ansaugtakt von kühlen Frischgasen umströmt und gekühlt werden, erreichen Ventilteller-Temperaturen bis über 500 Grad. Über 800 Grad heiß werden dagegen die Auslaßventile. Sie nehmen sowohl während des Verbrennungstaktes als auch während des Auspufftaktes Wärme auf. Die Kühlung erfolgt durch Wärmeabgabe am Ventilsitz und vom Ventilschaft an die Ventilführung.
Stahlventile werden zum Teil aus einem einzigen Material im Warmfließpressverfahren hergestellt. Häufiger bestehen sie dagegen aus zwei verschiedenen Stahlqualitäten. Diese sogenannten Bimetallventile erhalten einen hochwarmfesten Teller aus austenitischem Stahl und einen härtbaren martensitischen Stahl am Ventilschaft. Beide Teile werden getrennt vorgefertigt und anschließend im Reibschweißverfahren zusammengefügt.
Zur Verbesserung der Standfestigkeit sind die Ventilsitzflächen oft gehärtet oder gar mit speziellen Materialien gepanzert. Diese hochfesten Sonderlegierungen werden im Schmelzschweißverfahren aufgebracht. Ähnliche Härtungen oder Panzerungen erhalten auch die Ventilschaftenden, die hohen Flächenpressungen unterliegen. Zur Verbesserung des Laufverhaltens sind die Schäfte von Stahlventilen teilweise mit einer nur wenige tausendstel Millimeter dicken Hartchromschicht versehen oder durch spezielle Härteverfahren gegen Verschleiß geschützt.
Die aufwendigste Stahlventilart ist das Hohlventil, das fast ausschließlich auf der Auslaßseite eingesetzt wird. Bei diesem sehr teuren Ventil sind der Schaft und ein Teil des Tellers hohl. Der Hohlraum wird zu 60 Prozent mit metallischem Natrium gefüllt und anschließend mit einem Füllstück verschlossen. Das wärmeleitfähige Natrium schmilzt bei 97 Grad und hilft durch ständige Auf- und Abbewegung im Hohlraum während der Ventilbetätigung die Wärme vom Ventilteller an den Schaft weiterzuleiten. Die Temperaturabsenkung beträgt bis zu 120 Grad. Diese Ventile wurden früher besonders bei extrem belasteten Hochleistungsmotoren verwendet.
Heute werden im Rennsport Titanventile eingesetzt, dies bringt eine Gweichtsreduzierung gegenüber Stahl von 40 Prozent. Einige Hersteller experimentieren auch mit Keramik als Ventilwerkstoff, hier beträgt der Gewichtsvorteil sogar 60 Prozent. Je leichter die Ventile sind, desto höhere Drehzahlen beziehungsweise schärfere Steuerzeiten lassen sich realisieren.
Da der Zylinderkopf und die Bauteile des Ventiltriebs aus unterschiedlichen Werkstoffen bestehen, dehnen sie sich bis zum Erreichen der Betriebstemperatur unterschiedlich stark aus. Bei kaltem Motor muß daher ein Ventilspiel vorhanden sein. Zu großes Ventilspiel führt zu Klappergeräuschen und übermäßigem Verschleiß. Bei zu kleinem Spiel schließen die Ventile bei warmem Motor nicht mehr sauber und die Ventile können die Wärme nicht mehr an den Zylinderkopf weiterleiten. Durch die fehlende Wärmeabfuhr erhitzt sich der Ventilsitz so stark, daß er verbrennt. Das Ventilspiel wird üblicherweise über Einstellplättchen (Shims) oder -schrauben im erforderlichen Rahmen gehalten.
Mit minimalem Spiel und nahezu wartungsfrei arbeitet der hydraulische Ventilspielausgleich. Ein Ventilspielausgleichselement besteht aus einem Stößel, in dem ein weiterer Stößelkolben läuft. Bei Belastung, d. h. bei geöffnetem Ventil, ist der Ölraum zwischen beiden durch ein Kugelventil verschlossen. Die zu überwindende Kraft der Ventilfeder wird durch das Ölpolster übertragen. Tritt Ventilspiel auf, drückt eine Feder die Stößel auseinander. Durch das nun öffnende Kugelventil wird der Raum zwischen beiden Stößeln über die an die Schmierölversorgung angeschlossenen Bohrungen befüllt, bis das Ventilspiel ausgeglichen ist.
Der hydraulische Ventilspielausgleich ist in den Tassenstößel integriert. Bei Kipphebeln sitzt er am ventilseitigen Ende. Bei Schlepphebeln dient er als Lagerung des Hebels im Zylinderkopf.
Ventile mit gehärteten Schaftenden und Sitzen.
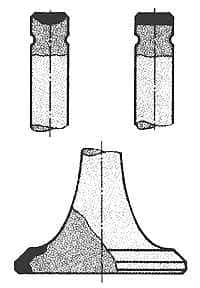
Ventilschaftenden und Ventilsitze sind gepanzert.
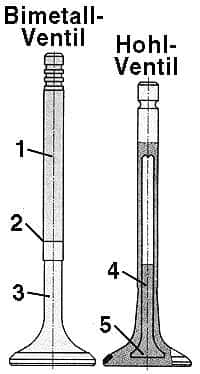
Schnittzeichnung eines Bimetall- und eines Hohlventils.
1=Schaftstück
2=Schweißnaht
3=Kopfstück
4=Natriumfüllung
5=Tellerhohlraum