Schon Thomas Alva Edison arbeitete mit Kohlefaser. 1881 erhielt der berühmte Erfinder ein Patent für die von ihm entwickelte Kohlefaserglühlampe mit Glühfäden aus speziell behandelten Bambusfasern. Als die Fäden später aus Metall gewonnen wurden, verschwand der schwarze Stoff in der Versenkung. Vorerst. In den Fünfzigern dann das Revival. Die Luftfahrtindustrie forderte leichtes und gleichermaßen festes Material für ihre Flieger – der Startschuss für eine außergewöhnliche Karriere. Doch erst in den späten achtziger Jahren entdeckte man Carbon auch fürs Motorrad.
Damals war die Substanz allerdings sehr schwer zu bekommen, und die Qualität ließ noch zu wünschen übrig. Heute ist das glücklicherweise anders. Jeder gute Zubehörhändler führt mittlerweile Teile aus Carbon, teils in erstklassiger Qualität. Doch woran erkennt man die? Und worauf muss man beim Kauf achten? Wie werden Carbonteile überhaupt hergestellt? Und wie der Grundstoff gewonnen? Diese und weitere Antworten liefern die folgenden Seiten. Damit das schwarze Material nicht die Grüne Minna auf den Plan ruft, vorab noch eine wichtige Information: Carbonteile aus dem Zubehör müssen in die Fahrzeugpapiere eingetragen werden. Oder man führt alternativ eine ABE mit sich. Das hätte es zu Edisons Zeiten freilich nicht gegeben.
Was ist Carbon?
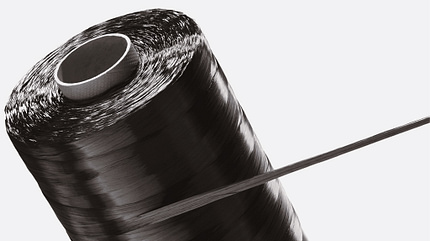
Carbon ist ein Verbundwerkstoff aus Kohlefasern und Kunststoff. Die einzelnen Fasern werden in einem thermo-chemischen Verfahren (Pyrolyse) aus kohlenstoffhaltigen Materialien gewonnen. Sie sind sechs- bis zehnmal dünner als ein menschliches Haar. Die Fasern werden zu einem Endlosstrang gebündelt, aufgespult und zu Matten gewoben. Beim Weben entsteht die charakteristische Netzstruktur, die sich bei Belastung nicht gegeneinander verschiebt.
Dadurch widersteht sie hohen Zugkräften aus jeder Richtung. Außerdem sehen Carbonmuster super aus. Vor der Verarbeitung werden die Matten in Kunstharz getränkt (Imprägnieren oder Laminieren) und in Formen gelegt. Zum Aushärten kommen die Formen in einen Ofen oder einen Autoklaven. Im ersten Fall spricht man von „Tempern“, im zweiten von „Backen“. Das ausgehärtete Material heißt carbonfaserverstärkter Kunststoff (CFK) oder auch kohlenstofffaserverstärkter Kunststoff (KFK). Oder schlicht Carbon.
Herstellungsprozess
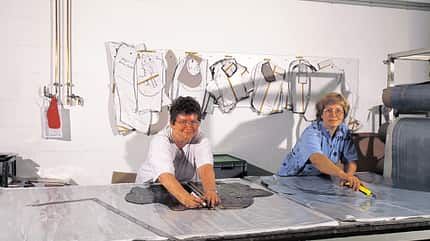
Reinigen der Form
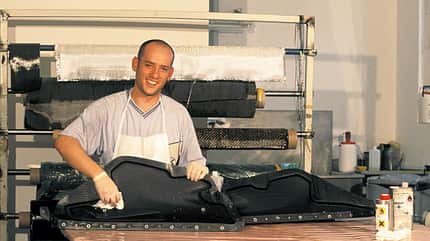
Nach dem Reinigen der Form wird der Zuschnitt darin ausgelegt.
Faltenfreies Einlegen der Matten
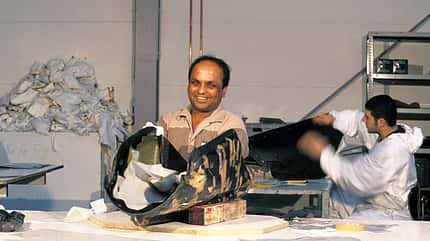
Dabei müssen die Arbeiter darauf achten, dass die Matten faltenfrei eingelegt werden.
Unterdrucksack
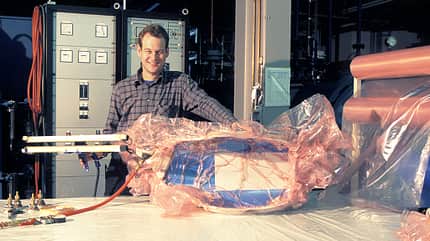
Der Unterdrucksack entzieht während des Backens überschüssige Bindemittel aus den Teilen.
Autoklaven
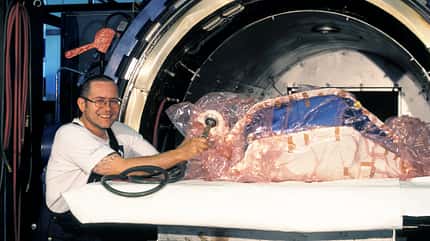
Im Autoklaven werden die Teile unter Druck und hohen Temperaturen gebacken.
Bauteil aus der Form lösen
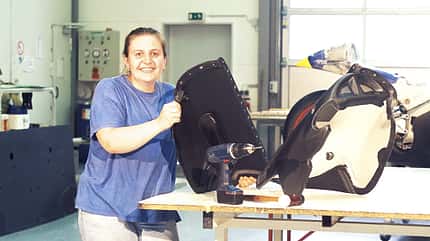
Nach dem Backen wird das Bauteil aus der Form gelöst.
Nachbehandlung mit Band und Exzenterschleifer
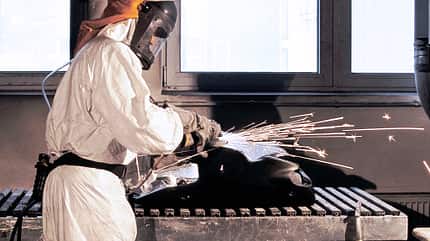
Nun folgt die Nachbehandlung mit Band- und Exzenterschleifer. Dabei schneidet ein Mitarbeiter die überstehenden Ränder ab, entgratet das Teil und bereitet es fürs Lackieren vor. Die Maske versorgt den Mann mit Frischluft.
Lackieren
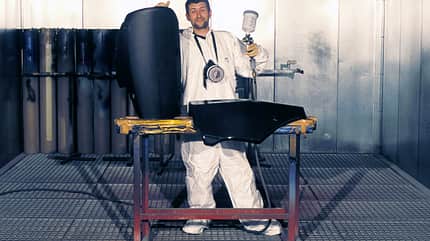
Letzter Schritt ist das Lackieren – meist mit Klar-, mitunter auch mit Buntlack. Oder als Kombination.
Verwendungsmöglichkeiten
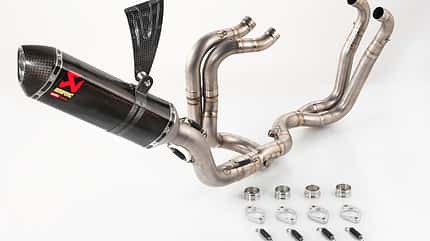
Sporthandschuhe
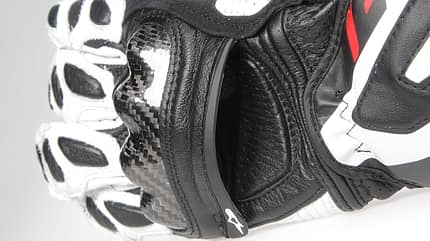
Beliebt sind Carboneinlagen bei Sporthandschuhen. Schlagtests bestätigten eine erhöhte Schutzwirkung.
Helme
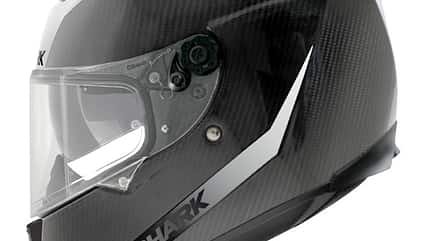
Mittlerweile führen die meisten großen Helmhersteller einen Kopfschutz aus Carbon.
Lenker
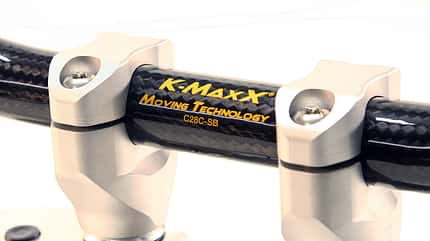
Als reines Kohlenstoff-Teil zu brüchig. Daher bestehen solche Lenker innen aus Alu und sind mit Carbon verziert.
Räder
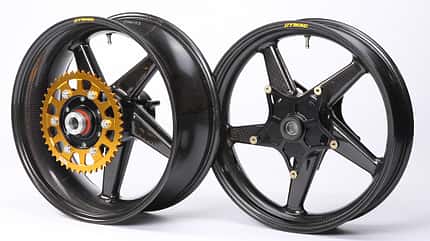
Besonders exklusiv sind Räder aus dem feinen Stoff. Bei Fahrtests litt allerdings mitunter die Fahrstabilität der Bikes.
Interview mit Julius Ilmberger
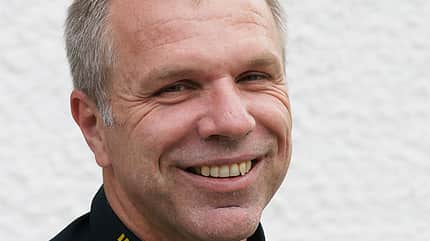
Julius Ilmberger ist Inhaber der Firma Ilmberger Carbonparts in Oberhaching bei München. Der ehemalige Racer ist seit jeher fasziniert von Carbon und gründete das Unternehmen 1990. Im PS-Interview erläutert der Spezialist alles Wissenswerte über das schwarze, leichte und edle Material.
Welche Vorteile hat Carbon außer Gewichtsersparnis eigentlich noch?
Carbon ist dank des strukturellen Aufbaus sehr stabil. Daher reißt es nicht so schnell wie beispielsweise glasfaserverstärkter Kunststoff, kurz GFK. Die Zähigkeit von Carbon schützt die darunterliegenden Teile sehr gut. Außerdem ist die Gefahr wesentlich geringer, dass der Motor oder Rahmenteile bei einem Sturz beschädigt werden.
Was spricht, außer dem Preis, gegen Fahrwerksteile wie Rahmen oder Schwinge aus Carbon?
Carbon ist im Wesentlichen nur auf Druck oder Zug belastbar. Deshalb ist es extrem wichtig, dass beim Aufbau der Teile die Laminatlagen in gewissen Richtungen zueinander gelegt werden, um die gewünschte Festigkeit zu erzielen. Bei Fahrwerksteilen verhält sich Carbon völlig anders als Aluminium oder Stahl, daher verändert sich die teils gewünschte Flexibilität von Rahmen oder Schwinge deutlich. Deshalb können solche Teile nicht einfach ausgetauscht und aus Carbon gefertigt werden. Aber es gibt Motorradrahmen aus Carbon, die hervorragend funktionieren.
Beim genauen Hinsehen fallen unterschiedliche Muster bei Carbonteilen auf. Wie kommt das?
Carbonmatten werden auf zwei Arten gewoben: Köper- und Leinwandbindung. In geringem Maße unterscheiden sie sich in der Zugfestigkeit, jedoch ist dies zu vernachlässigen. Zusätzlich zu Leinwand und Köperbindung wird auch noch nach Gramm unterschieden. Dies gibt dann die Größe und Breite der gewebten Fadenstränge an. Der Zubehörteilebau verwendet meist Köper oder Leinwand.
Wie werden die Matten weiter verarbeitet? Gibt es unterschiedliche Verfahren?
Grundsätzlich unterscheidet man zwischen Nasslaminieren und dem Gebrauch von sogenannten Prepreg-Matten. Im ersten Fall werden die Matten kurz vor der Verarbeitung in Harz getränkt und in eine Form gegeben. Danach kommt die Form zum Trocknen bei zirka 50 Grad in einen gewöhnlichen Ofen. Das nenne ich Tempern. Bei korrekter Umsetzung liefert diese Methode ordentliche Sichtergebnisse. Allerdings erzielt sie nicht die hohe Steifigkeit und Stabilität, wie sie beim Backen in einem Autoklaven erreicht wird. Außerdem kann man Nasslaminate wegen schlechter Oberflächenbeschaffenheit, Luft- und Harzeinschlüssen nicht so gut lackieren. Teilweise arbeiten Hersteller auch mit Presstechnik. Dabei wird das Gewebe mit einem Stempel in die Form gedrückt. Bis auf diesen Unterschied entspricht das Verfahren dem Nasslaminieren – mit den gleichen Nachteilen. Die Verwendung von Prepreg-Matten (Prepreg = „preimpregnatet fibres“, zu Deutsch: vorimprägnierte Fasern, die Red.) garantiert dagegen einen gleichbleibend niedrigen Anteil an Bindemitteln, da sie maschinell hergestellt werden. Dadurch sind die Bauteile sehr maßhaltig und haben eine klar definierte Stabilität.
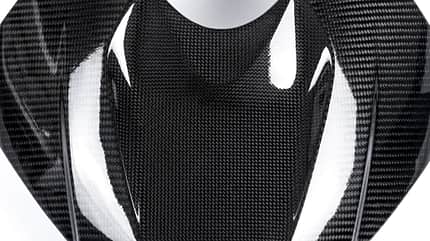
Müssen Prepreg-Matten noch nachlaminiert werden? Und härten sie mit der Zeit nicht von selbst aus?
Prepreg-Carbonmatten beinhalten bereits die nötigen Bindemittel und müssen nicht mehr, wie früher oder bei Nasslaminaten, mit Harz oder Ähnlichem getränkt werden. Wir verwenden je nach Anwendungsart verschiedene Prepreg-Gewebe mit unterschiedlicher Temperaturfestigkeit und unterschiedlicher Aushärtetemperatur und -dauer. Prepreg-Gewebe muss gebacken werden, um auszuhärten. Aber man sollte es in einem gewissen Zeitraum verarbeiten, sonst wird es unbrauchbar.
Sie haben beim Verarbeitungsprozess vorher von Autoklaven gesprochen. Was ist das genau?
Ein Autoklav ist ein gasdicht verschließbarer Druckbehälter, in dem Teile unter Druck und bei hohen Temperaturen gebacken werden.
Welchen Vorteil bietet diese Methode?
Wegen des Überdrucks wird das Gewebe stärker in die Form gedrückt, wodurch die einzelnen Laminatschichten stärker miteinander verbunden werden. Dadurch geraten die Teile deutlich stabiler als bei nur frei übereinandergelegten Lagen. Außerdem behalten die im Autoklaven hergestellten Teile ihre Festigkeit und werden nicht weich. Bei Nasslaminaten kann das bei Erwärmung passieren, beispielsweise durch Sonneneinstrahlung.
Welcher Druck und welche Temperaturen herrschen denn in einem Autoklaven?
Bitte haben Sie Verständnis, dass wir dazu keine genauen Angaben machen können. Aber ein Autoklav arbeitet in der Regel mit bis zu 10 bar Druck bei einer Temperatur von bis zu 250 Grad. Diese Grenzwerte müssen jedoch bei der Prepreg-Technologie nicht erreicht werden.
Vorm Backen im Autoklaven werden die Teile in Unterdrucksäcke verpackt. Wozu ist das nötig?
Ständiges Absaugen erzeugt einen bestimmten Unterdruck im Sack. Das entzieht die überschüssigen Bindemittel aus den Teilen. Zu viel Bindemittel und Harze stören die Stabilität von Carbon. Daher soll nur eine vorbestimmte Menge im Bauteil verbleiben.
Warum verwenden Sie Formen aus CNC-gefrästem Aluminium?
Aluformen sind zwar in der Herstellung sehr kostenintensiv, bieten aber den Vorteil, dass sie praktisch nicht verschleißen und eine gleichbleibende Qualität der Bauteile garantieren. Formen aus speziellem CFK sind problemlos möglich, aber sie bieten leider eine sehr begrenzte Lebensdauer und verschleißen stark.
Je stabiler ein Bauteil sein muss, desto mehr Lagen braucht es logischerweise. Aber aus wie vielen Lagen besteht denn beispielsweise die Seitenverkleidung eines Supersportlers?
Diese Frage lässt sich nicht generell beantworten. Die Anzahl der Lagen kommt auf den Bereich an. Besonders sturzgefährdete oder hochbelastete Flächen können auch mal fünf oder sechs Lagen aufweisen. Während wiederum in anderen Bereichen ein bis zwei Lagen ausreichend sein können.
Woran erkennt der Laie hochwertige Carbonteile?
Die Unterscheidung ist für Laien unter Umständen nicht einfach, denn es gibt teilweise sehr gut getarnte minderwertige Qualitäten. Hochwertige Carbonteile sind in sich sehr stabil und lassen sich im Verhältnis zur Stärke und zum Gewicht nur sehr schwer verformen. Nasslaminate erkennt man an der Oberfläche. Bei genauer Betrachtung fallen viele kleine Mikrolöcher auf. Es gibt auch zahlreiche Nasslaminat-Teile am Markt, die bereits mit Klarlack überzogen wurden. Die sind aber aufgrund der vielen Lackschichten verhältnismäßig schwer. Wie erwähnt, werden Nasslaminate zudem bei Erwärmung weich.
Teilweise werden GFK-Teile ja mit einer Kohlefasermatte überzogen. Im eingebauten Zustand ist das aber nur schwer von echten Carbonteilen zu unterscheiden, oder?
Das stimmt. Da in solchen Fällen aber meist nur die oberste Schicht aus Carbon besteht, kann man die GFK-Struktur auf der Innenseite gut erkennen. Auch dann, wenn sie schwarz eingefärbt ist. Außerdem sind solche Mixteile meistens sehr labil. Sie lassen sich durch einfaches Drücken der Oberfläche von echten Kohlefaserteilen unterscheiden. Komplett aus Carbon hergestellte Teile weisen außerdem auch auf der Innenseite die typische Struktur auf. Allerdings sieht diese etwas anders aus als auf der Oberfläche.
Als Versiegelung verwendet Ihre Firma Pulverbeschichtung. Warum arbeiten Sie nicht mit Spritzlack?
Die Kunststoffbeschichtung von Carbonteilen ist nicht üblicher Standard. In der Regel wird, wenn überhaupt, nur mit Spritzklarlack lackiert. Unsere Kunststoffbeschichtung sieht ähnlich aus wie dünner Klarlack, übertrifft diesen jedoch in der Stabilität und Kratzfestigkeit erheblich. Wir haben den erhöhten Schutz gegen Kratzer und UV-Licht nachgewiesen. Oft werden auch völlig unlackierte, nur polierte Teile auf dem Markt angeboten.
Ihre Firma genießt in der Szene einen erstklassigen Ruf und führt nach eigenen Angaben international mit seinen Carbonprodukten. Wie hoch ist denn ungefähr der Marktanteil in Prozent?
Wir sind in sehr vielen verschiedenen Bereichen aktiv. Deshalb ist es eher schwer, über Marktanteile zu spekulieren.