Eine Honda aus Atessa besteht aus etwa 1200 größeren Teilen. Zählt man jede Schraube, Scheibe und Mutter, sind es sogar rund 4000 Teile. Motorradproduktion bedeutet also, Tag für Tag 160 mal 4000 Teile, einzeln oder vormontiert, zur gleichen Zeit an den richtigen Ort zu bringen, wo sie von kompetenten Arbeitern zusammengefügt werden. An rund 250 Werktagen im Jahr.
Zugrunde gelegt sind dabei die eher niedrigen Produktionsziffern des Jahres 2010, als 40000 Motorräder in Atessa gebaut wurden. Nicht zu vergessen die 70000 Roller und 342000 Motoren für Rasenmäher, Stromaggregate oder Pumpen, die im gleichen Zeitraum dort entstanden. In den Jahren 2004 bis 2008 lag die Motorradproduktion knapp unter der 50000er-Schwelle, die Roller kamen in diesem Zeitraum auf 70000 bis 120000 Einheiten pro Jahr. Und an Motoren für sogenannte "power products" schuf das mittelitalienische Werk auch schon über 700000 Stück jährlich.
Der große Teile-Strom, der in Atessa zu Motorrädern verdichtet wird, speist sich aus vier Zuflüssen. Einer kommt aus der unmittelbaren Umgebung im Tal des Sangro. Dort hat sich seit dem Aufbau des Werks in den 1970er-Jahren ein Konsortium von Zulieferbetrieben angesiedelt und unter Federführung von Honda zusammengeschlossen. Gießereien, Galvaniken, Betriebe, die Kunststoffteile im Spritzgussverfahren herstellen, Blechteile pressen, auf CNC-Bearbeitungszentren Achsen oder Fittings entstehen lassen oder Kabelbäume flechten. Zweimal am Tag, um acht und um 14 Uhr, liefern sie ihre Produkte an, die sofort - just in time - verarbeitet werden.
Einen etwas weiteren Weg nimmt der zweite Teile-Zufluss. Komponenten, ja ganze Baugruppen wie Gabeln mitsamt Rädern bezieht das Honda-Werk von Betrieben aus Turin und Mailand, die seit den 1930er-Jahren im Dunstkreis von Fiat und den oberitalienischen Motorradherstellern entstanden sind. Laut italienischer Gesetzgebung gilt einbaufertiges Material nach zwei Tagen Liegezeit als Lagerbestand, der versteuert werden muss; die Räder in Bild Nummer drei, angeliefert am 6. Dezember und am 7. von MOTORRAD-Fotograf Markus Jahn abgelichtet, mussten noch am selben Tag eingebaut werden, da der folgende Tag in Italien ein Feiertag war.
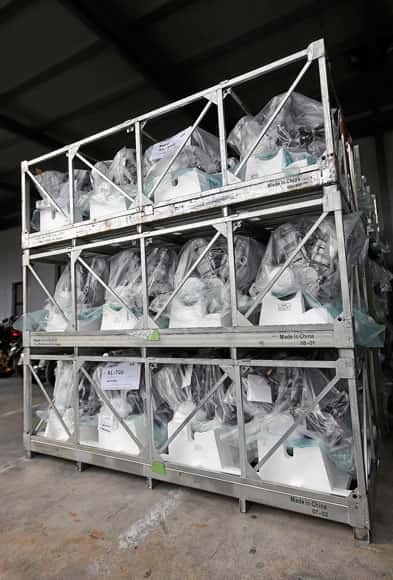
Der dritte Zustrom hat den weitesten Weg, er kommt mit zwei Wochen Vorlauf per Schiff vom Honda-Werk in Kumamoto auf der japanischen Südinsel Kyushu. Es handelt sich um alle Motoren mit mehr als 125 cm³ Hubraum, die 680er-V2 von Deauville (Kardanantrieb) und Transalp (Kettenantrieb), der 996er-V2 der Varadero sowie die Vierzylinder-Reihenmotoren mit 599 und 998 cm³ Hubraum, die in unterschiedlichen Ausführungen die CB- und CBF-Modelle sowie neuerdings die CBR 600 F antreiben (Foto-Show-Bild 1.). Der V2 der Varadero 125 wird zwar in Atessa zusammengesetzt, die Teile stammen jedoch ebenfalls aus Japan.
Die beiden Varadero nehmen wie die Transalp und die Deauville eine Sonderstellung ein. Ihre Fertigung wurde im April 2010 vom Honda-eigenen Montesa-Werk bei Barcelona nach Italien verlagert. So kommt es auch zu einer Sonderform der Teilelieferung, denn die Stahlrahmen der Transalp werden nach wie vor von Montesa in Spanien gefertigt. Wenn sie nach Atessa kommen, sind die zeitraubenden Schweißnähte an kleinen Blechhaltern oder Gewindebuchsen zwar schon ausgeführt, doch wegen geringerer Transportmaße und des Lagerhaltungsgesetzes geschieht das Verschweißen dreier Rahmenpartien und das Lackieren im italienischen Werk.
Bleiben als vierter Zufluss die dort vorproduzierten Teile. Die wichtigsten davon sind die Tanks und die Alu-Rückgratrahmen, die baugleich, aber mit unterschiedlichen Motorhalterungen und Lackierungen in allen Vierzylindermodellen eingesetzt werden. Nach Lackierung oder Pulverbeschichtung, Trocknung, Dichtigkeitsprüfung und Vormontage von Benzinpumpen oder Kleinteilen gelangen sie in großen Warenträgern per Gabelstapler an den Zusammenfluss der Ströme, das Produktionsband.
Hier werden alle Motorradmodelle in Losen von 60 Einheiten oder einem Vielfachen davon zusammengeschraubt. Sonderausstattungen wie ABS können von einem Los zum anderen eingebaut werden, anderes fest installiertes Zubehör ist als individuelle Ausstattung nicht vorgesehen. Mit höherer Taktzahl werden am zweiten, parallel laufenden Band die Rollermodelle montiert. Es herrscht ein pragmatisches Nebeneinander von Handarbeit und moderner Technik, aber Industrieroboter, die bei der Tankfertigung mit zackigen, ausholenden Bewegungen halbfertige Blechbehälter an eine Folge von Bandschleifmaschinen gehalten haben, sind hier nicht im Einsatz. Zwei Monteure, wie fast alle Kollegen bis hin zum Werksdirektor weiß gekleidet, stülpen den Doppelschleifenrahmen einer Varadero 125 über einen auf der rechten Seite liegenden Motor, drehen ihn wie einen Bajonettverschluss, bis die Montagepunkte an Rahmen und Motor fluchten und die eingesteckten Motorhaltebolzen in Position fallen. Ungeübte hätten da schon reichlich Lackschäden am Rahmen verur-sacht. Dann wird das Rohrgestell aufgerichtet, die Muttern werden aufgesetzt und mit Druckluft-Drehmomentschlüsseln festgezogen. Von innen nach außen, an später unzugänglichen Stellen zuerst, finden die Baugruppen zusammen, wenige Stationen weiter endet das auf Tischhöhe verlaufende Förderband, der Rohbau wird aufgehängt und ist damit bereit für die Aufnahme von weiter ausgreifenden Teilen wie Schwinge, Federlemente und Räder.
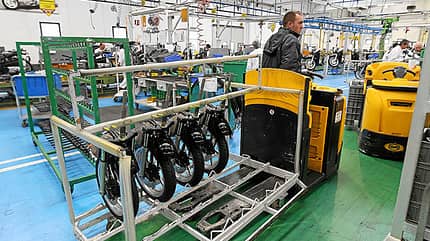
Weiter vorn erhalten die letzten Deauville des vorangegangenen Produktionsloses Kühl- und Bremsflüssigkeit aus einer einzigen Maschine. Innerhalb einer Minute sind Kühlkreislauf und Bremshydraulik befüllt und entlüftet; wer dies selbst einmal gemacht hat, kann ermessen, welche Zeit- und Geldersparnis die teure Spezialanfertigung mit sich bringt.
Nach der Montage kommt jedes Motorrad auf einen Rollenprüfstand, der Motor wird angelassen, die Gänge durchgeschaltet, Bremsen, Beleuchtung und alle Anzeigen überprüft. Das dauert 75 Sekunden, während jede Minute ein Motorrad vom Band gerollt wird. Der Prüfstand ist also der Flaschenhals; es wird kalkuliert, ob es sich lohnt, einen zweiten einzurichten. "Bei den derzeitigen Produktionszahlen hat diese Entscheidung noch Zeit", sagt Luca Fiorentino, Koordinator der "Quality Division", einer der obersten Qualitätskontrolleure.
Zwischen Prüfstand und Verladestation, wo die weit reisenden Motorräder in Kartons verpackt, die innerhalb Italiens ausgelieferten zwischen Schaumstoffmatten und Decken in den LKW verzurrt werden, steht alles voll frisch produzierter Maschinen. "Schon durch eine Farbänderung wird ein Motorrad für uns zu einem neuen Modell, dessen erste Serie durch eine fünfköpfige Gruppe hochrangiger Inspektoren genauestens geprüft wird", erklärt Fiorentino, "vorher können wir nicht ausliefern." Dann führt er die MOTORRAD-Delegation zu einem isoliert stehenden Gebäude, erteilt Fotografierverbot und zeigt eine Reihe von Messplätzen, Motoren-, Fahrwerks- und Belastungsprüfständen.
Teils dienen sie der Erprobung von Prototypen, teils der Kontrolle der laufenden Serie. Je ein Motorrad aus jedem Los, also jedes sechzigste wird statisch vermessen, dann werden die Lärm- und Schadstoffemissionen kontrolliert und zum Schluss kommt ein Fahrtest.
Darüber hinaus entwickeln und testen Fiorentino und seine Leute neue Fertigungsverfahren, zum Beispiel die Adhäsionskräfte einer Lackierung, und bereiten die Homologation von Neuentwicklungen vor.
Die Frage, wie viele Motorräder auf Garantie nachgebessert werden müssten, beantwortet er nicht. Diese Quote sei geheim. Doch als der Redakteur von einem anderen Motorradhersteller erzählt, der vier Prozent nicht nur toleriere, sondern fest einplane, weil jede weitere Verbesserung unverhältnismäßig teuer käme, entfährt ihm unwillkürlich die Frage: "So viel?" Man hat hier offenbar andere Maßstäbe.
Erfolgsgeschichte Honda
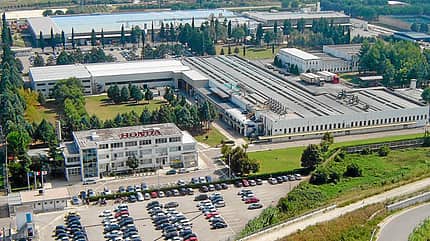
Im Jahr 1971 als I.A.P. industriale gegründet, wurde das Werk nach Verwicklung in einen Subventionsbetrug 1981 vollständig von Honda übernommen. Seit dieser Zeit hat sich der Standort zu einer funktionierenden Einheit entwickelt und in seiner Umgebung im Tal des Flusses Sangro eine vielfältig tätige Zulieferindustrie entstehen lassen. Heute ist das Werk in Atessa neben der 2008 in Betrieb genommenen Fabrik in Kumamoto die einzige Fertigungsstätte von Honda, in der Motorräder mit mehr als 300 cm³ Hubraum produziert werden. Ein Werk in den USA wurde geschlossen, bei Honda-Montesa in Spanien werden nurmehr Trialmotorräder und Zulieferteile hergestellt. In Atessa produzieren rund 700 Arbeiter im Einschichtbetrieb auf 44701 m² Hallenfläche neun Motorrad- und fünf Rollermodelle sowie zwei verschiedene Aggregatmotoren in je zwei Hubraumvarianten. Je nach Produkt schafft das Werk zwischen 10 und 50 Prozent der Wertschöpfung, der Umsatz betrug im Geschäftsjahr 2009 568,28 Millionen Euro. Etwa 63 Prozent der Produktion werden in Italien abgesetzt.
Drei Standbeine Hondas
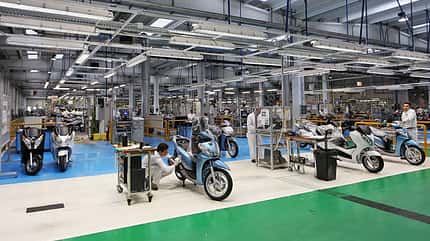
Mit der Motorradproduktion haben sie scheinbar wenig zu tun und doch sind sie ein stabilisierender Umsatzbringer für das italienische Werk: die Roller und die Aggregatmotoren, deren Bestandteile größtenteils im Werk selbst entstehen. Durch die Motorenproduktion kann das Werk die Saisonabhängigkeit im Motorradgeschäft ausgleichen, die Roller waren neben staatlichen Zuschüssen sogar einer der Hauptgründe für die Ansiedlung des Werks im Sangrotal. Durch die Nähe zu Rom, Neapel und anderen süditalienischen Großstädten, wo sie noch immer beliebt sind, sollten Transportkosten gespart werden. Und während die Produktion von Motorrädern und Motoren seit 2008 um mehr als die Hälfte zurückging, musste die Rollerfertigung deutlich weniger gedrosselt werden.