Es ist dieser kurze magische Moment, wenn das komprimierte Gemisch aus Sprit und Luft von der Zündkerze in Brand gesetzt wird, der unsere Leidenschaft entfacht. Wir erinnern uns an den ersten geglückten Startversuch mit dem eigenen Moped, das Knattern und Bollern, als wir die ersten Meter sozusagen „fremd-mobilisiert“ und in Windeseile die Straßen entlang gefegt sind. Was für ein Gefühl, einfach rechts am Griff drehen und ab geht die Post.
Was wir heute als selbstverständlich abhaken, ist bei genauer Analyse eines muskulösen Sportmotors die reinste Hölle. Warum? Weil sich das zusammengepresste Gemisch allein durch den Kompressionsdruck auf rund 500 Grad Celsius erhitzt, bevor der Zündfunke eine über 2000 Grad heiße Flammfront erzeugt. Dabei müssen Brennraum, Gemisch und Zündzeitpunkt so ausgelegt sein, dass das hochexplosive Gemisch eben nicht explodiert, sondern kontrolliert verbrennt. Doch selbst im optimalen Volllastbetrieb wird die Aluminium-Legierung des Kolbens auf über 300 Grad aufgeheizt, die der Kolben über die Ringe an die vom Kühlwasser umspülte Zylinderwand abgibt. Zusätzlich wird der Kolbenboden vom Kurbelgehäuse aus mit heruntergekühltem Motoröl bespritzt.
Die Detonation
Eine unkontrollierte Explosion des Luft/Benzingemisches – im Fachjargon der Motorenbauer auch als Detonation bezeichnet – würde durch die extreme Hitze und den kurzen, aber hohen Spitzendruck den Motor in wenigen Sekunden zerstören. Was dann vorkommt, wenn der Motor „nagelt“, sich das Gemisch also selbstständig entzündet. Dieser Zustand tritt dann auf, wenn das Verdichtungsverhältnis, der Zündzeitpunkt oder die Kraftstoffqualität (Oktanzahl) falsch gewählt sind. Als Folge schmelzen die Ränder des Aluminium-Kolbens oder die Mitte des Kolbenbodens. Um bei Serienmotoren die Verdichtung trotzdem so hoch als möglich ansetzen zu können – eine hohe Verdichtung bewirkt neben der hohen Leistung auch einen geringen Verbrauch und reduzierten Schadstoffausstoß –, kontrollieren bei vielen Motoren sogenannte Klopfsensoren die Verbrennung und regulieren bei Bedarf Zündung und Einspritzmenge.
Um möglichst kurze Flammwege zu erhalten, werden bei großvolumigen Zweizylindermotoren oftmals zwei Zündkerzen (Doppelzündung) verwendet, die dafür sorgen, dass das Gemisch auch an entlegenen Stellen vollständig verbrennt. Tut es dies nicht, entweichen die giftigen Kohlenwasserstoffverbindungen ungenutzt im Auslass. Bevorzugt „verstecken“ sich Gemischreste im Luftspalt des Feuerstegs oberhalb der Kolbenringe, weshalb dieses Volumen so klein als möglich ausfallen sollte.
Mehr als fünf Tonnen Spitzendruck
Extrem klein werden auch die meist umlaufenden Quetschzonen im Zylinderkopf angelegt. Dieser Trick sorgt dafür, dass sich das brennbare Gemisch in der Zylindermitte konzentriert und dort vollständig verbrannt wird. Erfahrene Tuner legen den Luftspalt der Quetschkanten so dicht an den Kolbenboden, dass es bei Höchstdrehzahlen zu einem ganz zarten metallischen Kontakt zwischen Kolben und Kopf kommen kann, der jedoch für die Haltbarkeit im Rennsport keine Rolle spielt. Zumal das Gaspolster bei Volllast regelrecht als Dämpfer zwischen Kopf und Kolben wirkt. So können bei Rennmotoren mit einem steifen Kurbeltrieb statisch gemessene Quetschkanten von 0,20 bis 0,30 Millimetern durchaus funktionieren. In der Großserie lassen sich solche grenzwertigen Auslegungen nur umsetzen, wenn Brennraum und Kolben durch eine präzise CNC-Bearbeitung exakt gefertigt sind.
Bei einer kontrollierten Verbrennung breitet sich die Flammfront nach der Zündung anfänglich mit lahmen 20 bis 30 Metern pro Sekunde aus, um dann auf rasante 200 m/s zuzulegen. Dabei wird ein Arbeitsdruck von rund 100 bar erzeugt. Übertragen auf die Fläche eines Kolbens mit 80 Millimeter Durchmesser (5027 mm²) wie bei der BMW S 1000 RR ergeben sich mehr als fünf Tonnen Spitzen-druck, die auf Kolben, Bolzen und Pleuel lasten. Der höchste Arbeitsdruck wird rund 15 Grad nach dem oberen Totpunkt erreicht.
Kolben weder rund, noch zylindrisch
Zu den extremen Gaskräften gesellen sich die Massenkräfte, denen Kolben und Pleuel bei 12 000/min ausgeliefert sind. Schließlich gilt es, den Kolben von einer Höchstgeschwindigkeit von rund 110 km/h, die er bei etwa halbem Hub erreicht, in nur etwas mehr als einer Tausendstelsekunde auf null abzubremsen oder wieder auf dieses Tempo zu beschleunigen. Der 250 Gramm leichte BMW-Kolben erreicht dabei eine dynamische Massenkraft von rund 6300 Newton, also einem Gewichtsäquivalent von mehr als 600 Kilogramm und somit dem 2500-fachen seines Eigengewichts. Ein triftiger Grund, Kolben so leicht als möglich zu konstruieren, zumal die oszillierenden Massen nicht nur Energie vernichten, sondern auch mehr oder weniger deftige Vibrationen erzeugen.
Um den extremen Drücken und Temperaturen bei Vollgas standzuhalten, sind Hochleistungskolben heutzutage als sogenannte Slipper- oder Kastenkolben konstruiert, während früher schwere Vollschaftkolben verbaut wurden. Dabei setzen die Techniker auf eine möglichst stabile Konstruktion aus Stegen oder Kästen, die den Kolbenboden zur Kolbennabe hin abstützen. Auch wenn es auf den ersten Blick so aussieht und für den Laien auch Sinn macht, sind Kolben weder rund, noch zylindrisch. Bedingt durch die unterschiedlichen hohen mechanischen und thermischen Belastungen ist die Kontur der Kolben entsprechend ballig und oval angelegt.
Die Zylinder
Die Zylinder selbst sind meist zur Reibungsminderung mit einer nur wenige Hundertstel Millimeter dicken Schicht aus einer verschleißfesten Silicium-Karbid-Nickel-Legierung überzogen. Graugussbuchsen findet man heute nur noch bei ganz billig gemachten Motorradmotoren.
Die Zylinderbohrung wird durch Honen absolut rund und zylindrisch gefertigt. Das Laufspiel zwischen Kolben und Zylinderwand beträgt bei wassergekühlten Motoren fünf bis acht Hundertstel Millimeter. Das Kühlwasser umströmt nur noch das obere Drittel der Zylinderbohrung, also den Bereich, in dem kritische Temperaturspitzen auftreten. Man reduziert dadurch die sogenannten Wandwärmeverluste, die dem Verbrennungsvorgang Energie entziehen und als nutzlose Abwärme den Verbrauch in die Höhe treiben.
Entscheidend für die Abdichtung speziell in unteren und mittleren Drehzahlen sind Konstruktion und Auslegung der Kompressionsringe. Früher aus empfindlichem Grauguss gefertigt, kommen heute üblicherweise zwei extrem schmale Stahlringe (0,75 mm) mit meist beschichteten Oberflächen und einer möglichst geringen Vorspannung zum Einsatz. Die geringe Auflagefläche der messerscharf geschliffenen Ringe sichert eine hohe Dichtigkeit, um den Verbrennungsdruck nicht als sogenanntes Blow-by ins Kurbelgehäuse entweichen zu lassen. Trotz der immens hohen Drücke rechnet man damit, dass nur rund ein Prozent der Gase den Weg ins Kurbelgehäuse findet. In der untersten Nut am Kolben sitzt der Ölabstreifring, oder besser die Ölabstreifringe, denn in modernen Motoren werden dort zwei nur noch etwa 0,4 Millimeter dicke Ölabstreifringe verbaut, in deren Mitte eine wellenförmige Bandfeder eingelegt ist, die das überschüssige Öl von der Zylinderwand über kleine Bohrungen in den Kolben und damit ins Kurbelgehäuse zurückleitet.
Reibung frisst Leistung
Die kurzen Kolbenhemden sorgen für geringe Reibung bei guter Führung und sorgen damit für einen mechanisch leisen Motorlauf. Dabei müssen die schmalen Kolbenhemden einiges aushalten, wenn der Kolben durch den Schrägstand des Pleuels mit heftiger Seitenkraft an die Zylinderwand gepresst wird. Diese Seitenkraft ist bei rund 15 bis 25 Prozent des Arbeitsdrucks angesiedelt. Weshalb nicht nur Rennkolben oftmals zur Reduzierung der Reibung mit einer Grafit/Kohlenstofflegierung beschichtet sind.
Entscheidend für die Seitenkraft ist neben dem Arbeitsdruck im Zylinder auch das Verhältnis von Hub zu Pleuellänge. Je kürzer das Pleuel, desto größer fällt die Seitenkraft aus, da das Pleuel stärker aus der Zylinderachse auslenkt. Je nach Einsatzzweck und Zielsetzung ergibt sich die passende Länge aus dem Verhältnis Hub zu Pleuellänge. Nimmt man das Beispiel unseres Parademotors der BMW S 1000 RR (Hub 49,7 mm, Pleuellänge 103 mm), ergibt sich ein Verhältnis von 0,48. Beim Kawasaki Z 1000-Motor (Hub 56 mm, Pleuellänge 106,2 mm) sind es 0,52, während bei Automotoren mit rund 0,3 die Pleuel im Verhältnis zum Hub deutlich länger, also auch schwerer ausfallen.
Pleuel bringen die Kraft erst ins Rotieren
Zur Reduzierung der Seitenkraft wird oft die Kolbenbolzenbohrung, die sogenannte Nabe, in Drehrichtung des Motors außermittig angebracht. Dadurch wird die Schrägstellung des Pleuels und damit die Seitenkräfte auf der Druckseite beim Arbeitstakt reduziert. Bei der Kawasaki Z 1000 beträgt dieser Versatz 0,5 Millimeter aus der Mittelachse. Das Pleuel ist generell in zwei Sektionen aufgeteilt, die jedoch fließend ineinander übergehen. Zum einen sind das die rotierenden Massen, die um den Pleuel-fuß gruppiert sind, und die oszillierenden Massen, zu denen der Schaft und das obere Pleuelauge gerechnet werden.
Um Gewicht im oszillierenden Bereich zu sparen, kann das obere Pleuelauge trapezförmig verjüngt werden. Im Auge selbst werden bei der überwiegenden Mehrheit der Großserienmotoren keine Gleitlagerbuchsen mehr verwendet. In diesen Fällen laufen Bolzen und Pleuel Stahl auf Stahl. Nach der reinen Lehre des Motorenbaus zählt diese Reibpaarung zu den schlechtesten, sie hat sich jedoch auch über lange Distanzen zumindest bei Vierzylindermotoren mit relativ kleinen Einzelhubräumen überraschend gut bewährt. Am Pleuel lässt sich am besten durch eine Titanlegierung Gewicht sparen. Aufgrund der etwas geringeren Festigkeit des leichten Werkstoffs müssen zwar die Dimensionen leicht erhöht werden, dennoch ist eine Gewichtsersparnis von rund 40 Prozent garantiert.
Werkstofflegierung und Herstellungsverfahren
Die Form des Pleuels kann je nach Werkstoff, Geometrie und Philosophie der Hersteller anders ausfallen. Die Doppel-T- Struktur des Pleuelschafts tragen jedoch alle geschmiedeten Stahlpleuel, mit Ausnahme der sogenannten Messerpleuel, wie sie überwiegend bei älteren Zweitakt-Rennmotoren verwendet wurden. Bei gefrästen Titanpleueln hingegen steigert ein H-Querschnitt die Biegesteifigkeit. Eine Form, die sich bei den geschmiedeten Großserienteilen nicht durchgesetzt hat. Entscheidend für die Festigkeit des Pleuels, das einer permanenten Zug-Druck-Wechselbelastung ausgesetzt ist, sind die Werkstofflegierung und das Herstellungsverfahren. Bei Hochleistungsmotoren werden die Pleuel aus Vergütungsstahl im Gesenk geschmiedet. Dabei bliebt der Faserverlauf des Werkstoffs erhalten, womit die Bruchgefahr deutlich vermindert wird.
Am Pleuelfuß, der die gelenkige Verbindung zur Kurbelwelle herstellt und deshalb mit zwei Halbschalen aus einem Dreistofflager ausgekleidet ist, wird der Pleueldeckel verschraubt. Dazu werden zwei hochfeste Dehnschrauben verwendet. In den meisten Fällen sind diese Deckel zusammen mit dem Pleuel nach dem Schmieden bearbeitet und garantieren durch Passstifte oder Passschrauben den absolut korrekten Sitz der Lagerschalen. BMW hingegen setzt auf sogenannte „gecrackte“ Pleuelfüße. Dabei wird nach der Bearbeitung die Lagerbohrung durch einen Gewaltbruch aufgesprengt, wodurch die Bruchstellen eine absolut passgenaue Struktur erhalten und so ohne Passhülsen auskommen. Pleuel wie Kolben werden gewogen und durch Markierungen einer spezifischen Gewichtsklasse zugeordnet. Diese Angleichung sorgt für einen möglichst weichen und geschmeidigen Massenausgleich und einen vibrationsarmen Motorlauf.
Technische Grundlagen und Tipps
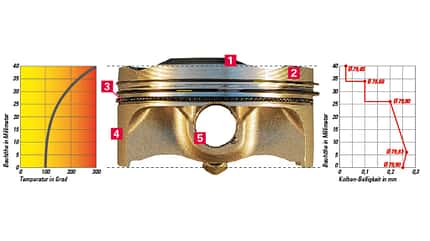
1) Der Kolbenboden
Er ist der höchsten Temperatur ausgesetzt (siehe Diagramm links oben) und überträgt den gesamten Verbrennungsdruck. Seine Form richtet sich nach Winkel und Größe der Ventile sowie der gewünschten Quetschkante. Zudem gibt er die sogenannte Kompressionshöhe (Abstand von Kolbenbolzenzentrum bis Kolbenboden) vor.
2) Der Feuersteg
Auch hier entstehen hohe Temperaturen und eine entsprechend große Materialausdehnung, weshalb der Kolbendurchmesser in diesem Bereich reduziert wird (siehe Diagramm rechts oben). Entsprechend stark ist die unbedenkliche Ölkohleablagerung.
3) Die Ringzone
Hier sitzen üblicherweise zwei Kompressionsringe und ein Ölabstreifring in den eingedrehten Ringnuten. Auch dieser Bereich wird noch sehr heiß und ist entsprechend im Durchmesser reduziert, weshalb sich in diesem freien Raum unerwünschte Frischgase „verstecken“.
4) Das Kolbenhemd
Das Kolbenhemd übernimmt die Führung im Zylinder und soll das Kolbenkippen reduzieren. Im direkten Kontakt mit der Zylinderwand kann es hier zu Verschleiß und Fressspuren kommen. Rund zehn Millimeter vor dem unteren Rand hat der Kolben seinen größten Durchmesser, weshalb an dieser Stelle das Kolbeneinbauspiel gemessen wird.
5) Die Kolbennabe
In ihrer feinbearbeiteten Bohrung sitzt der Kolbenbolzen. Er wird links und rechts von Sicherungsclips fixiert.
Tipps und Tricks
Mit Tuning nach Hausmacher-Art ist im Bereich Kolben/Pleuel nichts zu machen. Hier können nur die wenigen, wirklich guten Tuner und Teilelieferanten weiterhelfen. Lediglich bei der Anschaffung von Neuteilen lassen sich gewisse Toleranzen aus-
sortieren, vorausgesetzt, man hat genügend Teile zur Auswahl. Bei den Kolbenringen werden zum Beispiel die Teile mit dem geringsten Stoßspiel bevorzugt, bei Kolben und Pleuel sollte das Gewicht identisch sein. Ein nachträgliches Beschichten von Kolbenbolzen und Kolbenhemden mit Kohlenstoff hilft die Reibung zu reduzieren und Leistung freizusetzen.
Beim neuen Beschichten der Zylinder lässt sich die Dichtigkeit im Bereich der Ringzone dadurch erhöhen, dass sich die Zylinderbohrung nach oben hin um rund 3/100 MiIlimeter konisch verjüngt. Was jedoch nur in Absprache mit der jeweiligen Spezialfirma zu machen ist.