Schalldämpfer unterscheiden sich in zwei Bauarten: Es gibt einerseits Reflexionsdämpfer, die den Schall durch verschiedene Kammern im Innern der Anlage dämpfen. Und andererseits Absorptionsdämpfer, die etwa 95 Prozent des Markts abdecken und bei denen um das Innenrohr gewickelte Dämmwolle für die erforderliche Geräuschreduktion sorgt. 2Räder ließ sich bei Shark den Herstellungsprozess der wesentlich häufiger verwendeten Absorptions-Modelle zeigen.
Rund 20 eifrige Mitarbeiter sorgen seit 1981 dafür, dass aktuell zirka 15000 Endtöpfe pro Jahr den Betrieb verlassen. Wen wundert’s – schließlich gehört der Anbau eines Zubehör-Dämpfers zu den beliebtesten Umbaumaßnahmen am Motorrad. Warum? Ganz einfach: Die meisten Serienanlagen sind klobig, schwer und nicht gerade hübsch. Außerdem bleibt ihr Sound häufig auf der Strecke. Nahezu alle Nachrüstdämpfer aus dem Zubehör sind schlanker, zierlicher, wirken sportlicher – auch was den Sound anbelangt –, sind meist wesentlich leichter und kosten weniger als der Serientopf.
Arbeitsschritt 1
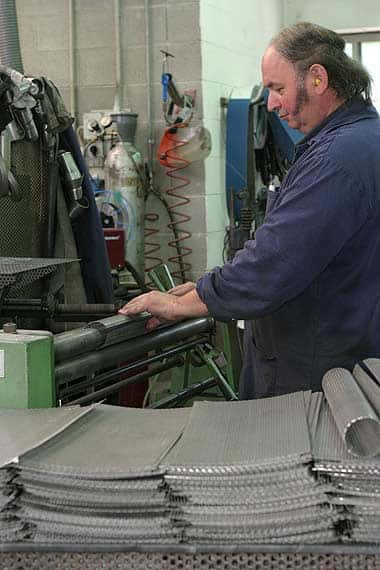
Riesige Lochbleche aus Edelstahl werden im ersten Arbeitsschritt zunächst auf die benötigte Größe zurechtgeschnitten und dann an einer Maschine zu einem Rohr gerollt.
Arbeitsschritt 2
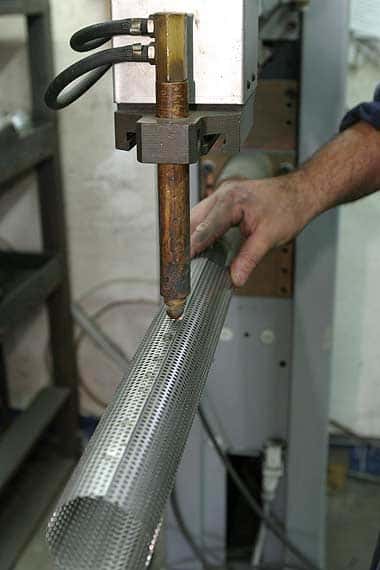
Jede Menge Schweißpunkte über die gesamte Länge des Lochblechs sorgen dafür, dass das spätere Innenrohr stets in Form bleibt.
Arbeitsschritt 3
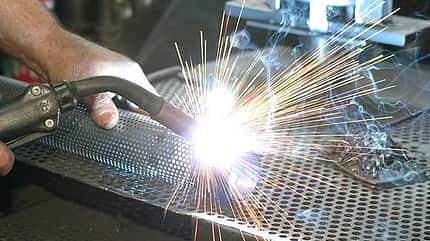
Zum Auspuffende hin wird ein kurzes Metallröhrchen eingeschweißt, das später als Führung für den dB-Absorber (auch Flöte genannt) dient.
Arbeitsschritt 4
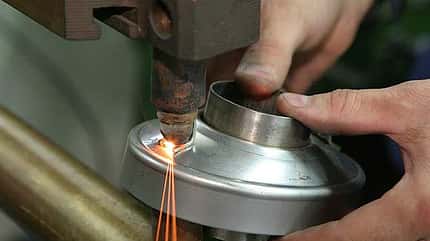
Auf die vordere Endkappe zum Krümmer hin werden zwei Metallhaken aufgeschweißt, in die man bei der Auspuffmontage die Sicherungsfedern einhängt.
Arbeitsschritt 5
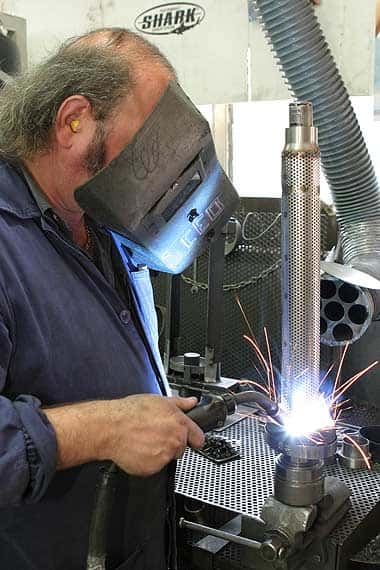
Nun wird die vordere Kappe mit den angebrachten Federhaken mit dem gelochten Innenrohr verschweißt.
Arbeitsschritt 6

Ein Mitarbeiter wickelt Dämmstoff aus hitzebeständigem Glasfasermaterial in mehreren Lagen möglichst straff um das gelochte Innenrohr.
Arbeitsschritt 7
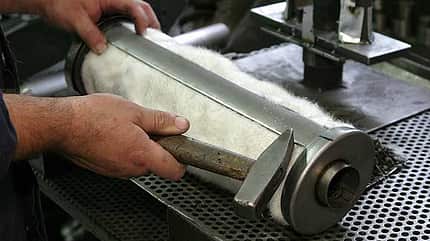
Nach dem Anschweißen der innenliegenden hinteren Endkappe wird eine schmale Stahlstrebe eingefügt und verschweißt. Sie dient später als Befestigung für den Auspuffhalter.
Arbeitsschritt 8
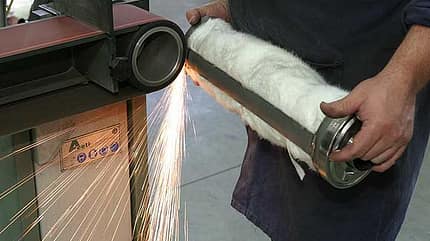
Damit sich die Außenhülle aus Aluminium, Edelstahl, Karbon oder Titan ungehindert über den Rohling schieben lässt, muss die überstehende Schweißnaht abgeschliffen werden.
Arbeitsschritt 9
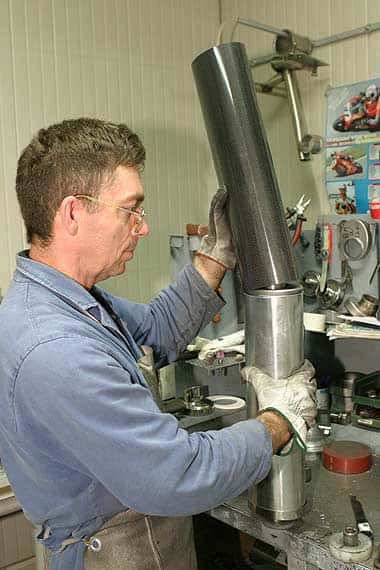
Bevor die Karbon-Außenhülle aufgeschoben wird, erhält der Rohling noch eine Hitzeschutzschicht aus Spezial-Textil und Aluminiumblech.
Arbeitsschritt 10
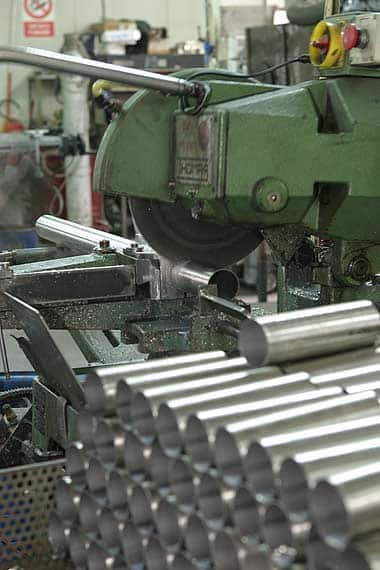
Die sichtbaren, hinten aus dem Auspuff ragenden Endröhrchen, die mit der außen liegenden Abdeckkappe verschweißt werden, müssen aus Stangenmaterial mit einer Kappsäge auf die benötigte Länge gebracht werden.
Arbeitsschritt 11
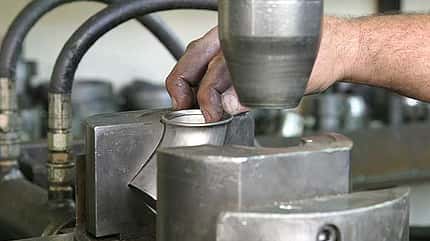
In mehreren Arbeitsschritten wird das Endröhrchen auf Spezialpressen gebogen und umgebördelt. Dadurch sieht das Rohrende nicht nur hübsch aus, es weist auch keine scharfkantigen Grate mehr auf.
Arbeitsschritt 12
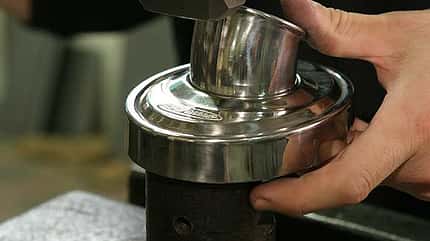
Die Endkappe, die bereits mit dem gebogenen Endröhrchen verschweißt wurde, erhält durch einen Prägestempel Markenlogo und e-Kennzeichnung.
Arbeitsschritt 13
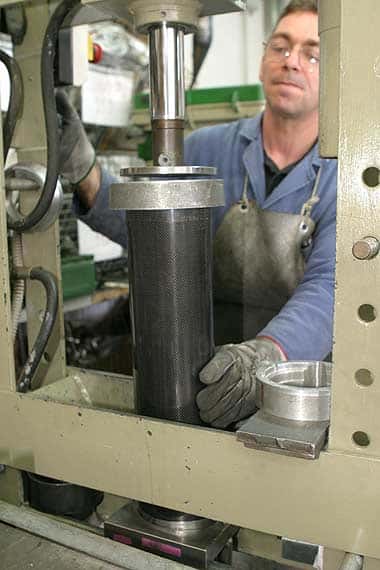
Mit Maschinenkraft wird die fertige hintere Endkappe über die Außenhülle des Schalldämpfers gepresst. Um die empfindliche Karbonhülle nicht zu beschädigen, ist Fingerspitzengefühl gefragt.
Arbeitsschritt 14
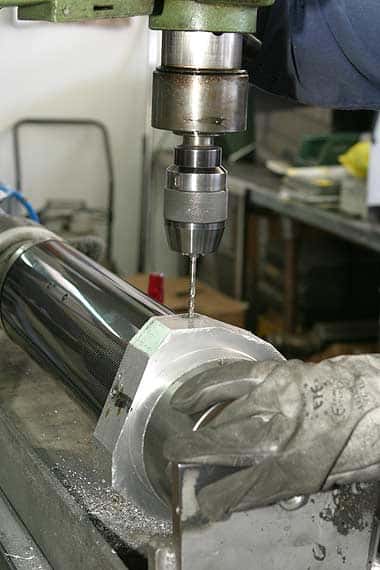
Die fast fertigen Schalldämpfer wandern in Schablonen, um die Löcher für Auspuffhalter sowie für sämtliche Nieten der Endkappen und des Markenlogos zu bohren.
Arbeitsschritt 15
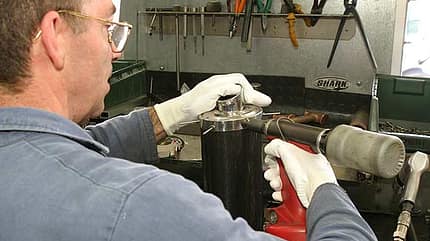
Für das Vernieten der Endkappen benötigt ein Montageprofi mit Hilfe einer bewährten Nietpistole nur wenige Sekunden. Und schon hält der Topf zusammen.
Arbeitsschritt 16
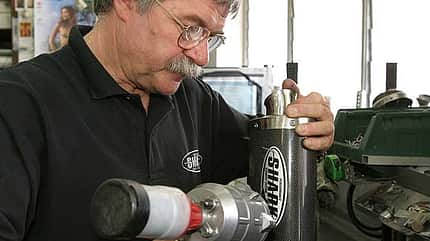
Aus Anlass des 2Räder-Besuchs ließ es sich der Firmenchef nicht nehmen, höchstpersönlich das Firmenlogo anzubringen.
Arbeitsschritt 17
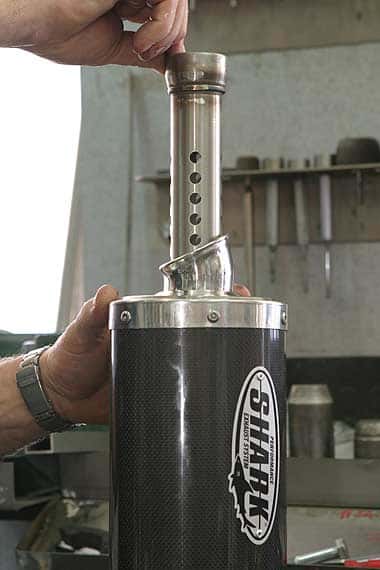
Nun noch den dB-Absorber einführen und vernieten, und fertig ist der Schalldämpfer. Abschließend reinigt und poliert die Versandabteilung den Topf, steckt ihn in einen passenden Karton und verschickt ihn.