Wissen Sie, wie viel Stress ein abgefahrener Reifen bedeutet? Natürlich müssen Sie jetzt loslegen: informieren, welcher Reifen wohl der Beste für Ihr Bike ist, Tests lesen, Preise vergleichen, Räder ausbauen, zum Händler laufen, montieren lassen… Doch drehen wir das Rad noch ein paar Runden weiter zurück. Ein paar Tausend Kilometer stecken nun in den Gummis. Dabei haben sie im Alltag allerhand wegstecken müssen: Längs- und Querkräfte haben sie malträtiert, bucklige Asphaltbänder sie gestaucht und gequetscht. Sie waren frostigen Temperaturen im Frühjahr und Herbst ausgesetzt und aufgeheizten Asphaltbändern im Hochsommer. All das haben sie unbeschadet überstanden und immer genügend Haftung geboten. Auf einer Auflagefläche, die gerade einmal einer 20-Cent-Münze entspricht. Das schwarze Gold hat es wirklich in sich, aber was steckt noch alles dahinter?
Zunächst die Erfindung des luftbefüllten Gummireifens durch den Schotten John Boyd Dunlop. Das ist inzwischen 125 Jahre her, und die Weiterentwicklung hat definitiv die Mobilität auf der ganzen Welt beeinflusst. Im Laufe der Zeit wurden zahlreiche Neuerungen für Motorradreifen eingeführt: Niederquerschnittsreifen, Schlauchlosreifen, Radialreifen … Dunlop selbst, so heißt es, ist durch seine Erfindung nicht reich geworden. Doch die Firma, die seinen Namen trägt, prägt bis heute das Reifenbusiness in aller Welt mit.
Das Dunlop-Zentrum liegt in Frankreich
Für die Entwicklung der Motorradreifen von Dunlop ist das Reifenwerk im französischen Montluçon die zentrale Anlaufstelle. Um die Gründung im Jahr 1920 rankt sich übrigens eine nette Anekdote: Um den stark wachsenden Bedarf an Reifen zu decken, suchte Dunlop Anfang des letzten Jahrhunderts nach neuen Standorten. Im Süden Frankreichs hatte man bereits eine geeignete Fläche ins Auge gefasst. Doch auf dem Weg dahin quittierte die Dampflok ihren Dienst – ausgerechnet in dem Städtchen Montluçon in der Auvergne. Während der Reparatur schauten sich die Dunlop-Ingenieure den Ort an und stellten fest, dass genau hier, mitten in Frankreich, der perfekte Platz für das neue Reifenwerk war. Wer heute die Fabrik betritt, fühlt sich im ersten Augenblick auch um dieses eine Jahrhundert zurückversetzt. Maschinenungetüme prägen die Hallen, es stinkt nach Gummi und Lösungsmitteln. Doch das ist nur vordergründig so.
Natürlich steckt immer noch viel Knochenarbeit in der Herstellung eines modernen Motorradreifens. Doch im Detail bestimmen inzwischen sehr viele Hightech- und Präzisionsgeräte die Produktionsabläufe. Selbst bei der Herstellung des künstlichen Kautschuks, dessen Qualität permanent durch ein direkt an die Fertigung angegliedertes Labor überwacht wird. Da hier in Frankreich das synthetische Gummi auch für weitere Dunlop-Werke in aller Welt entsteht, wären die Folgen bei eventueller Abweichung von den Produktionsvorgaben fatal. Präzision ist auch gefragt, wenn es um den Aufbau der Karkasse geht: Dazu wird der Kautschuk mit einer überdimensionalen Nudelteigmaschine auf exakte Breite und Dicke ausgerollt, auf eine Wickeltrommel aufgebracht und mit Textil- und Kevlareinlagen stabilisiert. Zur Verstärkung kommt schließlich das sogenannte „Jointless Belt“-Verfahren (JLB) zum Einsatz, bei dem ein Draht exakt in Laufrichtung ausgerichtet („Null-Grad-Gürtel“) auf die Karkasse aufgespult wird. An den nächsten Stationen werden weitere Einzelteile des Reifens konfektioniert. Einlagen aus gedrillten Stahldrähten bilden die Wulst des Reifens, wichtig für den festen Sitz auf der Felge.
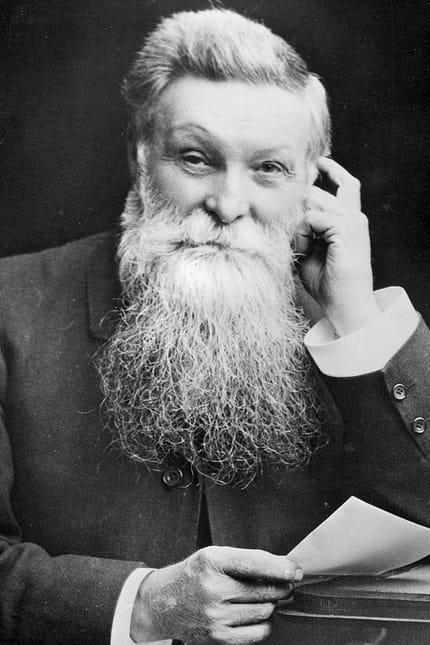
Die Karkasse wird schließlich von Hand zusammengefügt. Die Wulstkerne werden dabei über das Karkassengewebe gestülpt, die Ränder umgeschlagen und mit der Karkasse verklebt. Wenn schließlich noch die Reifenflanken aufgelegt werden und die Wickeltrommel den kompletten Verband kräftig aufbläht, ist die Nähe zu einem späteren Motorradreifen unverkennbar. Ein echter Clou ist das Aufbringen der Lauffläche: Wurden die Laufstreifen früher wie eine Matte aufgelegt, kommt nun das „Jointless Tread-Verfahren“ (JLT) zum Einsatz, das ein wenig an das Aufsprühen von Sahne auf eine leckere Torte erinnert. Durch das Aufspulen will man bei Reifen mit unterschiedlich harten Gummimischungen („Multicompound“) diese möglichst exakt auf der Lauffläche positionieren. Ein Verfahren, nach dem übrigens auch alle Rennreifen für die Moto2-WM von einer baugleichen Maschine in Birmingham gefertigt werden.
Schließlich ist der Pneu bereit für die Vulkanisation, bei dem die einzelnen Bestandteile des Motorradreifens miteinander verbunden werden. Dazu wird der noch weiche Reifen in eine heiße Form gegeben, die innen mit einer Membran versehen ist. Diese Membran wird mit heißem Wasser gefüllt und presst den Reifen mit hohem Druck in die Form. Dabei entstehen auch gleichzeitig das Reifenprofil und die Beschriftung der Flanken.
Der Vulkanisationsprozess dauert zirka 20 Minuten. Autoreifen benötigen nur zehn Minuten. Aber es ist der komplexe Aufbau und die hohe mechanische Beanspruchung eines Motorradreifens, die diesen langen Vulkanisationsprozess erfordert. 640 Mitarbeiter produzieren pro Tag 3710 Motorradreifen in den Größen von 13 bis 21 Zoll. Das entspricht einer Jahresproduktion von über 1,3 Millionen Reifen. Und das ist wahrlich keine Luftnummer.