Einer der modernsten Produktionszweige, ja quasi das Herz des BMW-Motorradwerks in Berlin-Spandau, ist die mechanische Fertigung. Dort entstehen die wichtigsten Teile des Doppelnocken-Boxers, des 200 PS starken Vierzylinders der S 1000 RR oder des brandneuen Sechszylinders. Doch die hochpräzisen Bearbeitungszentren, millionenteure Maschinen auf dem neuesten technischen Stand, stehen in denkmalgeschützten Hallen. "Wenn wir hier eine neue Maschine aufstellen wollen und dafür einen Wanddurchbruch vergrößern, müssen wir die Wand Stein für Stein wieder originalgetreu aufbauen", erzählt Dr. Stefan Kasperowski, der Leiter der Abteilung. Er sagt dies mit einem gewissen Stolz, keinesfalls macht es den Eindruck, als sei ihm dieser Aufwand lästig. Offenbar empfindet er ähnlich wie der Besucher, der den Anfang einer langen Tradition und ihre allerneueste Ausprägung in ein und demselben Gebäudekomplex treffend symbolisiert sieht.
Ein gedeihliches Neben- und Ineinander von neu und alt herrscht auch bei den Produktionsstrategien. Prozessorgesteuerte Automatisierung in allen Spielarten und Handarbeit werden pragmatisch kombiniert. Hierin unterscheidet sich BMW nicht von Honda und nicht einmal von Bimota, wo die in reiner Handarbeit montierten Teile ja auch von Zulieferbetrieben maschinell gefertigt werden. Gemeinsam haben die drei so unterschiedlichen Motorrad-Produktionsstätten auch, dass dort mehr Handarbeit geleistet wird, als in der Automobilbranche, wo weitaus höhere Stückzahlen gefragt sind.
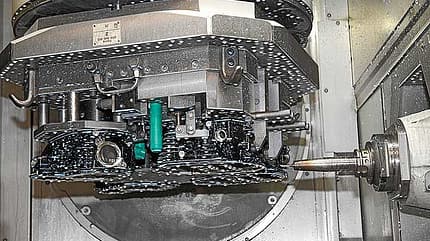
In den historischen Hallen reibt und fräst ein Bearbeitungszentrum mit nur einem Werkzeug die Ventilführungen und -sitze eines S 1000 RR-Motors mit einer Toleranz von maximal 4 tausendstel Millimeter. Gleichzeitig werden gegenüber, in der Halle der Motorenmontage, die Ventilspielwerte eines fast komplettierten K 1600-Sechszylinders von Hand mit der Fühlerblattlehre gemessen. Oder die Pleuelfüße und -schrauben eines weiteren S 1000-Motors behutsam mit einer Verlängerung und einem Torx-Einsatz aufeinander angesetzt, bevor ein automatischer Doppelschrauber sie auf ein Grunddrehmoment und mit einem einheitlichen Drehwinkel dann endgültig festzieht. Den Zwischenschritt haben die Mechaniker selbst eingeführt, als sie entdeckten, dass es zu Passungsproblemen kommen kann, wenn die individuelle Bruchstruktur eines jeden Pleuelfußes zu flach ausfällt und die Schrauben rasch angezogen werden.
In der Lackiererei vollführen Roboter, die zum Schutz ihrer Mechanik vor Farbnebeln in elastische Trikots gehüllt sind, komplizierte Sprayer-Choreografien, bevor die frisch gespritzten Teile die Trocknungsprozedur durchlaufen. Parallel dazu werden an 20 Arbeitsplätzen lackierte Teile von Hand mit Klebedekors versehen oder mit Klebeband nach exakt vorgegebenen Mustern teilweise maskiert und so für eine zweite Schicht mit Klarlack oder einen weiteren Farbton vorbereitet. Farbschemata wie etwa die weiß-blau-rote Rennsportlackierung der S 1000 RR brauchen gar drei Durchgänge: Erst werden die Verkleidungsteile weiß lackiert, dann nach einer Maskierung blau und schließlich nach dem Aufbringen der roten Dekorstreifen mit Klarlack. Verständlich, dass dieser Aufwand auch Aufpreis kostet.

In allen Abteilungen erzählen deren Leiter von den neuesten Verbesserungen im Produktionsablauf, die sie mit ihren Mitarbeitern entwickelt haben. Als im Krisenjahr 2009 die Produktion gedrosselt wurde, nutzten die Arbeiter der mechanischen Fertigung die frei gewordene Zeit und spielten mit Kartons und leeren Gitterboxen, die Werkzeugmaschinen darstellen sollten, neue Anordnungen und Abläufe durch. Am Ende hatten sie einen Prozess entwickelt, der bei der Zylinderkopfbearbeitung ein Viertel der Durchlaufzeit spart. In der Motorenmontage oder an den einzelnen Fertigungsbändern sind alle nötigen Kleinteile, Schrauben, Muttern, Schellen oder Dichtungen wie in einem Supermarkt ausgebreitet. Die Anordnung dieses Supermarkts ist aber von Abteilung zu Abteilung verschieden. Mal in Reihen nach der Abfolge der Arbeitsgänge sortiert, mal in U-Form dargeboten, aber immer so, wie diejenigen es für optimal halten, welche täglich damit umzugehen haben. Jeder ist aufgerufen und eingeladen, an einem permanenten und bis ins Kleinste gehenden Optimierungsprozess teilzunehmen. Im Vergleich der Motorradwerke von BMW und Honda fällt hier ein wichtiger Unterschied auf: Ein Prozess, dessen Funktionalität bewiesen ist, wird bei BMW sofort wieder kritisch betrachtet und bei Honda erst einmal respektiert. Das schließt nicht aus, dass man bei BMW manches beim Alten lässt und bei Honda vieles neu macht, zeigt aber eine völlig andere Grundeinstellung.
Ein weiteres Alleinstellungsmerkmal von BMW erfordert eine komplizierte Logistik: die Möglichkeit, jedes Motorrad je nach Wunsch und Budget mit einer Vielzahl von Sonderzubehör und Sonderausstattungen ausrüsten zu lassen. Bis drei Tage vor der Montage können die Kunden ihre Auswahl ändern. Dann muss die jeweilige Spezifikation im System festgelegt werden. An drei Grundmontagebändern mit den schon berühmten gelben L-Trägern werden dann die verschiedenen Modelle der K-, R- und S-Baureihe so weit zusammengebaut, bis sie fahrfertig sind. Was nicht heißt, dass sie schon komplett wären, obwohl die meisten individuellen Ausstattungsmerkmale sich in diesem Stadium bereits an Bord befinden. Die Aufteilung auf die drei Bänder erfolgt nicht streng nach Baureihen getrennt. Zwar entstehen alle K-BMW, egal ob 1300 oder 1600, an einer Fertigungslinie; das bietet sich wegen der Ähnlichkeiten einfach an. Die Boxer-Modelle werden aber auf zwei Bänder verteilt, wobei die aufwendig verkleidete RT und ihre Behördenversion mit der ebenfalls vollverkleideten Supersportlerin S 1000 RR vom gleichen Band laufen. Die sparsamer verschalten GS- und R-Varianten teilen sich das dritte. Alle F 800 und die G 650 GS entstehen auf sogenannten Flexbändern, das sind keine klassischen Fließbänder, sondern rollende Träger, die von Station zu Station geschoben werden.
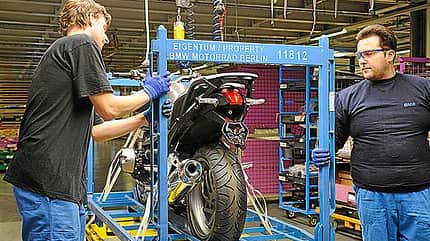
In diesem Stadium, in dem die Komponenten noch relativ leicht erreichbar und nötigenfalls zu tauschen sind, durchlaufen alle Motorräder einen aufwendigen Funk-tionstest. Allein beim ABS werden über 100 Parameter geprüft. Dann werden die Maschinen auf vier Endmontagebänder verteilt, wobei nach Zeitaufwand für die Endmontage sortiert wird. Eine R 1200 erhält dort nur noch Sitzbank und Seitendeckel. "Am aufwendigsten sind die Behördenfahrzeuge mit Funkgeräten, Sirenen, Blaulichtern und aller möglichen Ausrüstung. Die verbringen hier im Extremfall bis zu drei Stunden. Das ist die hohe Schule", sagt Franz-Xaver Burgmaier, Leiter dieser Abteilung. "Deshalb arbeiten dort auch unsere besten Leute. Sie müssen eine lange Abfolge von Arbeitsschritten beherrschen."
Sowohl vor der Montage als auch zwischen Fertigstellung und Versand ist die Batteriepflege eine wichtige Sache. ABS, elektronische Fahrhilfen und das Bus-System, das mitunter hohe Ruheströme fließen lässt, funktionieren nicht unterhalb der definierten Mindestspannung; entsprechend oft werden Batterien nachgeladen.
Auf dem Weg zum Versand bekam die MOTORRAD-Delegation zufälligerweise eine Ahnung davon, wie viel Vorbereitungszeit es braucht, die Produktionsstätte für ein neues Modell einzurichten. Eine mit Tuch verhüllte Maschine, die aus einer Halle geschoben wurde, erwies sich bei einem kurzen Windstoß als Großroller nach Art des "Concept C", im letzten Herbst als "Designstudie" vorgestellt. Nun, diese Designstudie geht wohl nach den Werksferien im August 2011 in Serie.
Standort mit Tradition
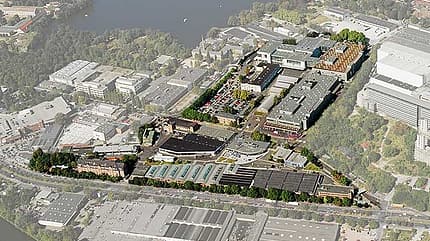
Die ältesten Hallen des Spandauer Werks stehen schon seit 1928, seit 1939 gehört es zu BMW. Doch erst 1969, mit der neu entwickelten /5-Baureihe begannen die Bayern, dort Motorräder zu produzieren. Damals wurden die Kapazitäten in München für die Automobilproduktion gebraucht, außerdem gab es satte Investitionszulagen, um die eingeschlossene Stadt Berlin wirtschaftlich am Leben zu erhalten. Letztlich halfen sie BMW, trotz des damals flauen Markts die Motorradfertigung nicht aufzugeben. Heute bauen etwa 1600 Arbeiter im Berliner Werk um die 100000 Motorräder pro Jahr, bis zu 550 am Tag. Saisonale Schwankungen gleicht die Belegschaft durch flexiblen Schichtbetrieb und Arbeitszeitkonten aus. 2010 investierte BMW 35 Millionen Euro in den Ausbau des Werks.
Überblicksdarstellung dreier Hersteller
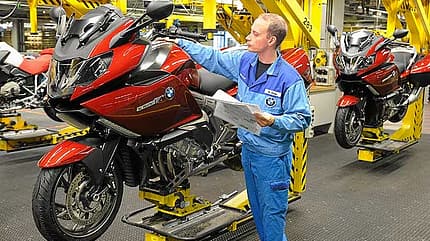
MOTORRAD stellte die Produktionsstätten dreier Hersteller vor. Zum Abschluss ein Vergleich von Zahlen und Fakten.
Motorrad-Produktion kann viele verschiedene Ausprägungen annehmen. Neben den teilweise enormen Unterschieden faszinierte bei den Werksbesuchen vor allem, wie sich die momentane Situation des jeweiligen Herstellers in den Aktivitäten vor Ort widerspiegelte. Honda agiert angesichts sinkender Marktanteile sehr vorsichtig, Bimota kämpft ums Überleben und BMW investiert und expandiert. Neben zahlreichen neuen Modellen setzen die Bayern dabei noch stärker als früher auf ein umfangreiches Angebot an individuell wählbaren Sonderausstattungen.
Fehlt nur noch eine Reportage über das Herz der Honda-Produktion: das neue Werk im japanischen Kumamoto. Die Anfrage läuft.
Hersteller | BIMOTA (Rimini/Italien) | BMW (Berlin) | HONDA (Atessa/Italien) | Gründungsjahr | 1973 | 1939 | 1971 |
Mitarbeiter insgesamt/ Motorradbereich | 25/25 | ca. 1900/ca. 1630 | ca. 700/ca. 700 | Arbeitszeit-regelung | Einschichtbetrieb | Zweischichtbetrieb/ Arbeitszeitkonten | Einschichtbetrieb |
Motorrad- Jahresproduktion 2010 | ca. 190 Einheiten | 97076 Einheiten | 40000 Einheiten und 70000 Roller | Motorrad-Gesamtkapazität | ca. 600 Einheiten | ca. 130000 Einheiten | ca. 66000 Einheiten und 132 000 Roller |
Produktions-segmente | Entwicklung, Test und Montage | Entwicklung von Produktionsverfahren, mechanische Fertigung, Motorenmontage, Rahmenbau, Tankfertigung, Lackierung, Montage | Entwicklung von Produktionsverfahren, Rollermotorenbau, Rahmenbau, Tankfertigung, Lackierung, Montage | Anzahl Modelle | 6 | 17 | 9 Motorrad- und 5 Rollermodelle |
Sonstige Aktivitäten | Tests im Auftrag anderer Hersteller | Bremsscheiben- fertigung für BMW-PKW | Aggregatmotorenbau |