Wer im Innovationspark Wackersdorf zum ersten Mal vor den langen Regalreihen des „Supermarkts“ steht, reibt sich die Augen. Anstatt der erwarteten Fahrzeugteile sieht man erst einmal nur fliederfarbene Kisten. Die Boxen stapeln sich in allen möglichen Größen und bilden einen schrillen Kontrast zum Industriegrau ringsum. Der Motorrad-„Supermarkt“ belegt rund 4.000 der insgesamt 20.000 Quadratmeter großen Halle der „BMW-Auslandsversorgung“. Von hier aus verschickt der Konzern 21.500 nach Sachnummern sortierte Teile von BMW-Fahrzeugen in alle Welt, die meisten verpackt als CKD-Fahrzeugbausätze. Das Kürzel steht für „completely knocked down“, also völlig zerlegt – oder besser gesagt: noch nicht vollständig zusammengebaut. Den Löwenanteil machen hierbei Autos aus. Doch seit einigen Monaten verschickt BMW von Wackersdorf aus auch Motorrad-Bausätze, die denen der Autos eine ausgeklügelte Logistik voraus haben: das „Bike-in-the-Box“-System. Aber dazu kommen wir noch.
Denn erst einmal wollen wir wissen, was es mit den fliederfarbenen Kisten und dem Supermarkt auf sich hat. „Ganz einfach, die Farbe kennzeichnet, dass die Kisten uns gehören“, erklärt Standortleiter Thomas Dose. Das soll verhindern, dass BMW-eigene Transport- und Lagermaterialien irrtümlich an einen der 1.450 Zulieferer der Auslandsversorgung zurückgehen. Und der Begriff Supermarkt hat sich als Name für den Lagerbereich der Motorradteile durchgesetzt – weil die langen Regalreihen entfernt an einen Discounter erinnern.
"Bike-in-the-Box"-Prinzip
Aber zurück zu den Motorrad-Bausätzen aus Wackersdorf. Nach dem Completely-knocked-down-Prinzip exportiert BMW von hier aus bereits seit Ende 2009 Motorräder nach Manaus für den brasilianischen Markt – und für den asiatischen seit Ende 2013 ins BMW-Montagewerk nach Rayong in Thailand. Damit werden die hohen Einfuhrzölle für Komplettfahrzeuge umgangen, ein in der Fahrzeugindustrie global übliches System. Und dieses System hat bisher so funktioniert, dass alle Teile im sogenannten „Zwölfer-Abgriff“ verschickt wurden: je zwölf Rahmen, zwölf Motorblöcke, zwölf Scheinwerfer, zwölf Fußbremshebel, zwölf Sitzbänke usw. fanden den Weg aus den Lagerregalen in die Kartons und gingen anschließend in Übersee-Containern per Schiff in Richtung Brasilien oder Thailand. Die Innovation aus dem Wackersdorfer Innovationspark ist nun, dass dessen Packer eigens für den CKD-Export von Motorrädern das Prinzip des „Bike-in-the-Box“ entwickelt haben. Thomas Dose erklärt den Unterschied so: „Im Grunde funktioniert das wie bei Ikea: Wir packen ein Paket. Da ist dann für den Kunden alles drin, was er braucht, um es aufzubauen. Nur sortieren wir alle Teile auch gleich so in den Karton, wie sie bei der Montage gebraucht werden.“ Vereinfacht gesagt: ein Motorrad – eine Kiste. Doch so simpel, wie die Grundidee klingt, war ihre Umsetzung keineswegs.
Die Realisierung von „Bike-in-the-Box“ lief unter der Regie von Projektleiter Christoph Peters. Er erzählt: „Bevor wir die Idee entwickelt haben, den Versand nach dem Bausatz-Prinzip anzubieten, haben wir uns die Abläufe der Montage in Brasilien und in Thailand gründlich angesehen. Dann haben wir überlegt, wie man den ganzen Prozess besser und effektiver gestalten kann.“ Und am effektivsten ist wohl, wenn alle für ein Motorrad benötigten Teile möglichst beieinander sind. Und nicht nur das: „Das Teil, welches zuerst gebraucht wird, kommt zuletzt in die Kiste. Entsprechend liegt es beim Auspacken ganz obenauf“, erklärt Peters. Dafür müssen die Teile in Deutschland sortiert und nach genauen Vorgaben, welches wo zu liegen hat, verpackt werden. Was natürlich einen gewissen Mehraufwand zum bisherigen System bedeutet. Das bestätigt Innovationsparkleiter Thomas Dose: „Das Packen in Deutschland dauert pro Motorrad etwa eine Stunde länger.“ Doch der Mehraufwand rentiert sich unterm Strich. Denn, so Dose: „Dafür sparen wir in der Montage vor Ort ganze fünf Stunden ein.“
Mit dem Rollwagen durch den "Supermarkt"
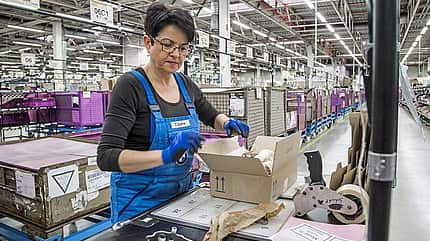
Und wie funktioniert das Einpacken jetzt ganz genau? Wir fragen eine, die es wissen muss: Dagmar Dudova ist eine von 13 Wackersdorfer Packerinnen und Packern, die sich ausschließlich um die Motorradteile für das „Bike-in-the-Box“ kümmern. Sie hat soeben über die interne EDV den elektronischen Auftrag bekommen, die Teile einer BMW F 800 GS für Thailand zusammenzustellen. Auf ihrem Rollwagen hat sie einen Laptop, der nicht nur alle benötigten Teile-Nummern für die Zweizylinder-Reiseenduro vorgibt, sondern auch mittels Scannererfassung kontrolliert und bestätigt, dass die soeben von Dagmar Dudova in die Box gelegte Benzinpumpe auch die richtige ist. Je nach Modell sortiert die Packerin so bis zu 131 Teile nach einer genau festgelegten Reihenfolge in die dafür vorgesehenen Fächer in vier übereinander angeordnete Lagen in den Karton. Der begleitet sie auf dem Rollwagen von Station zu Station durch den eingangs erwähnten „Supermarkt“ – wie sie den Wagen durch dessen Regale schiebt, erinnert tatsächlich ein wenig ans Einkaufen. Am Ende bestätigt der Rechner, dass Dagmar Dudova alle benötigten Teile eingepackt hat. Der Karton wird geschlossen, mit den richtigen Labels versehen und auf einer Palette im Warenausgang abgestellt. Von dort geht’s anschließend mit dem Gabelstapler erst in den Container, dann auf den am Gleisanschluss längsseits der Halle schon bereitstehenden Güterzug und schließlich von Wackersdorf aus auf der Schiene nach Bremerhaven.
Der eben beschriebene Ablauf klingt nun so einfach, dass man sich fragt, warum man das bei BMW nicht gleich von Anfang an so gemacht hat. Weil der Ablauf ganz so einfach eben doch nicht ist. Schließlich, so erklärt Projektleiter Peters, gibt es an jedem Motorrad auch Teile, die nicht eben mal so verschickt werden können, sie stellen nämlich Gefahrgut dar: „Batterien etwa, oder gasdruckbefüllte Federelemente.“ Die müssen weiterhin separat verpackt werden, genauso übrigens die Räder, Rahmen, vormontierten Motoren und die Farbteile, also die lackierten Verkleidungskomponenten. Das „Bike-in-the-Box“ geht noch farblos auf die lange Reise. Sie dauert von Bremerhaven aus auf dem Seeweg rund sechs Wochen.
CKD-Anteil noch unter 10 Prozent
Ob dabei nicht auch mal etwas schief oder verloren geht, wollen wir noch wissen. Beim Verpacken und Versenden so gut wie nie, erklärt Innovationsparkleiter Thomas Dose. Die Fehlerquote liege bei 0,03 Fehlern pro Fahrzeug (Auto und Motorrad). Und falls unterwegs tatsächlich einmal etwas verloren gehen sollte, so käme ein weiterer Vorteil des „Bike-in-the-Box“-Prinzips zum Tragen. „Früher war es so: Hat eine Kiste gefehlt, war davon auf einen Schlag die Montage von 12 oder 24 Motorrädern betroffen. Heute ginge es in so einem Fall nur um ein einziges Motorrad.“
Wie viele Motorräder BMW als Teilebausätze von Wackersdorf aus exportiert, darüber gibt der Hersteller keine Auskunft. „Derzeit beträgt der CKD-Anteil an der Gesamtproduktion noch unter zehn Prozent“, erklärt BMW-Pressesprecher Rudi Probst. Das wären demnach nicht mehr als jährlich gut 10.000 „Bikes-in-the-Box“, wahrscheinlich weniger. „Allerdings werden wir die Auslandsfertigung mittelfristig deutlich ausbauen“, ergänzt Probst. Und Kapazitätsgrenzen sind in Wackersdorf längst nicht erreicht, wie Standortleiter Thomas Dose betont. Hier ist also Luft nach oben drin. Auch wenn die Kartons mit Teilen randvoll sind.
Der Standort
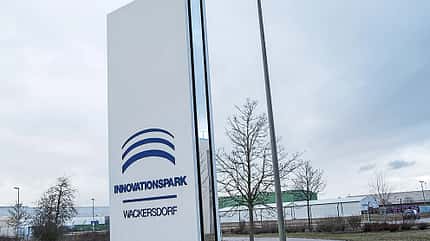
Wackersdorf? Da war doch was … Richtig. Vor genau 30 Jahren tobten in der kleinen Gemeinde 40 Kilometer nördlich von Regensburg regelrechte Schlachten zwischen Gegnern der dort geplanten atomaren Wiederaufbereitungsanlage (WAA) und der Polizei, die das Baugelände im Taxöldener Forst schützen sollte. Nach der Katastrophe von Tschernobyl verschärften sich die Proteste, bis im Mai 1989 die Betreibergesellschaft überraschend das Aus für die WAA verkündete – aus finanziellen Gründen. Die Anlage wurde nie fertiggestellt.
Im Juli 1989 sagte BMW seine Ansiedlung auf der frei gewordenen Industriefläche zu, startete 1990 dort eine Pkw-Karosseriefertigung. In den Folgejahren wuchs ringsum ein Industriepark mit Zulieferern und Joint-Venture-Unternehmen. Das BMW-Versorgungszentrum für die Auslandsfertigung entstand, und BMW startete die Produktion von Auto-Cockpits. Seit 1998 heißt der BMW-Standort Innovationspark Wackersdorf. Das ehemalige WAA-Brennelemente-Eingangslager (im Bild das grüne Gebäude im Hintergrund) dient heute als Materiallager für temperatursensible Rohstoffe der Karbonfertigung – die meterdicken Mauern sorgen für stets gleiches Innenraumklima.