Wann wird ein Ventil geöffnet, wie schnell und wie weit? Wie lange bleibt es offen, wie rasch wird es wieder geschlossen? Diese Werte sind fundamental wichtig für die Leistung und Effizienz von Viertaktmotoren, und von wenigen Ausnahmen abgesehen werden sie durch die Form der Nocken auf der Nockenwelle bestimmt. Keine Nocke drückt jedoch direkt auf ein Ventil. Weil dessen Schaft aus Gewichtsgründen so dünn wie möglich ausgeführt sein muss, würde die Nocke ihn schon beim ersten Anlaufen irreparabel verbiegen. Deshalb befindet sich zwischen der Nocke und dem oberen Ende des Ventilschafts immer mindestens ein Betätigungselement. Klein, oft unscheinbar, sind diese Betätigungselemente doch enorm wichtig für die Funktion eines Motors.
2 Anforderungen an Ventilbetätigung
Trotz allem Streben nach geringem Gewicht kann ein Ventil kein massefreies Bauteil sein, und es muss bei der überwiegenden Mehrzahl aller Viertaktmotoren gegen die Kraft der Ventilfeder(n) aufgedrückt werden. Aus diesen simplen Tatsachen ergeben sich zwei hauptsächliche Anforderungen an eine effiziente Ventilbetätigung:
1.) Die bewegten Massen müssen möglichst gering sein, um Trägheitsmomente zu minimieren und somit schnelles Öffnen und Schließen der Ventile zu erlauben. Je schneller und weiter ein Ventil bewegt werden kann, desto größer wird der Gasdurchsatz und damit die Leistung.
2.) muss die Kontur der Nocken präzise auf die Ventile übertragen werden, die Ventilbetätigung also möglichst steif sein. Wenn bei jeder Ventilbetätigung ein Teil der aufgewendeten Kräfte in der Elastizität des Systems verpufft, zum Beispiel durch seitliches Wegbiegen einer Stoßstange, werden die Steuerzeiten nicht präzise eingehalten, und der Motor braucht mehr Leistung, um sich selbst am Laufen zu halten, anstatt ein Fahrzeug anzutreiben.
Höhere Steifigkeit der Ventilbetätigung lässt sich zwar prinzipiell mit mehr Materialeinsatz erreichen, doch der macht wiederum die Teile schwerer. Man sieht: Nur äußerst clevere Konstruktionen können beide Anforderungen in befriedigender Weise erfüllen.
Mechanik ist heute simpler
Die Entwicklungsgeschichte der Ventilbetätigungen ist Teil einer viel breiter angelegten Entwicklung der Viertakttechnik hin zu immer höheren Drehzahlen, mehr Leistung, sparsamerem Verbrauch, geringerem Schadstoffausstoß, geringerem Gewicht, kompakterer Bauweise, höheren Laufleistungen bei noch vertretbaren Produktionskosten. Je mehr diese einander widersprechenden Entwicklungsziele in Einklang gebracht werden mussten, desto mehr entsprachen die Elemente der Ventilbetätigung den oben formulierten grundsätzlichen Anforderungen.
Besonders faszinierend ist dabei der Umstand, dass die Konstruktionen im Lauf der Entwicklung nicht unbedingt komplizierter geworden sind. Eine ohv-Ventilbetätigung mit Stößel, Stoßstange und Kipphebel erfordert mehr mechanischen Aufwand als eine Ventilbetätigung über Tassenstößel. Selbst Schlepphebel modernster Prägung, wie sie die BMW S 1000 RR und Yamaha YZF-R1 besitzen, kommen mit relativ simpler Mechanik aus. Hier steckt allerdings ein enormer Aufwand in der Bearbeitung und Beschichtung der kleinen oszillierenden Hebelchen. Bei näherem Hinsehen erweisen sie sich als faszinierende Teile.
Membranventil, stehendes Ventil, Stoßstange
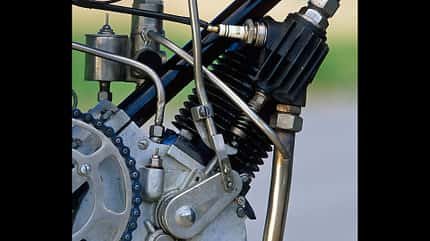
Die NSU von 1902 hatte einen Zedel-Motor mit einem Membran- oder Schnüffelventil im Einlasstrakt. Solange der abwärts gleitende Kolben genügend Unterdruck produzierte, um die metallene Membran „aufzusaugen“, konnte Gemisch in den Brennraum strömen. Das stehende Auslassventil musste dagegen von einer Nocke gesteuert werden; es wurde über eine kurze Stoßstange betätigt. Das Streben nach mehr Leistung brachte höhere Drehzahlen, Temperaturen und Verbrennungsdrücke mit sich; sie brachten das Schnüffelventil im Einlass an seine Grenzen und darüber hinaus. Die Konstrukteure erkannten die Notwendigkeit, auch im Einlass nockengesteuerte Ventile zu verwenden. Diese Entwicklung vollzog sich im Lauf weniger Jahre.
Stehende Ventile, Kipphebel, Stoßstange
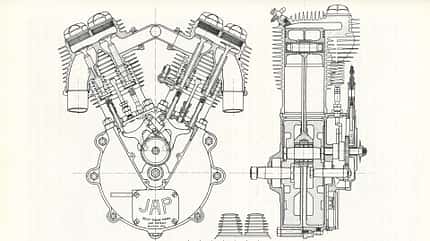
Beim seitengesteuerten JAP-V2 aus den frühen 1920er-Jahren steuerte eine kurze Nockenwelle mit nur einer Ein- und Auslassnocke alle vier Ventile. Möglich wurde dies durch aufwendige mehrarmige Kipphebel im Steuergehäuse auf der linken Motorseite. Die Kipphebelarme übertrugen die Nockenkontur auf kurze Stoßstangen, welche wiederum auf die Schäfte der stehenden Ventile drückten. Eingebaut wurden die Ventile durch Bohrungen auf der Oberseite des Zylinderkopfes. Nach der Montage wurden diese durch eingeschraubte Stopfen verschlossen. Zwecks besserer Kühlung gab es als Option hoch bauende Stopfen mit Kühlrippen, regelrechte „Kühltürme“.
Kipphebel, Stoßstange
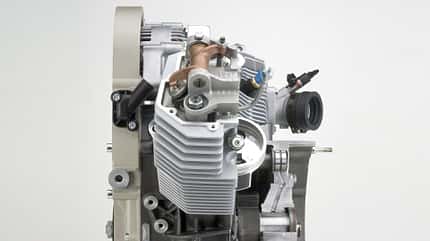
Die BMW-Zweiventiler, die ehrwürdigen englischen Reihenzweizylinder von BSA über Norton bis Triumph, die Big Twins und Sportster-Motoren von Harley, die V7- und V9-Motoren von Moto Guzzi – alle setzten auf die Ventilbetätigung über Stoßstangen und Kipphebel. Meist sitzt zwischen Nocke und Stoßstange auch noch ein Stößel. Der Vorteil dieses Prinzips liegt in der geringen Bauhöhe der Zylinderköpfe und den kurzen Übertragungswegen des Nockenwellenantriebs. Nachteilig wirken sich die aufwendige Mechanik, die vergleichsweise schweren bewegten Massen und die Durchbiegung der oft langen Stoßstangen aus. Drehzahlen von über 8000/min sind deshalb mit einem ohv-Ventiltrieb in der Großserie auf Dauer kaum möglich. Das Prinzip ist heute ein Fall für eher gemütliche Motoren.
ohc, Kipphebel
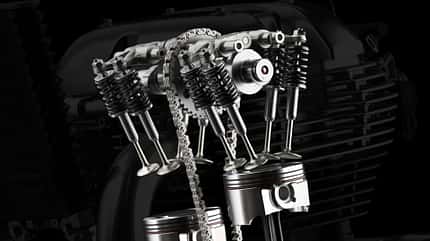
Die Ventilbetätigung über eine obenliegende Nockenwelle und Kipphebel vermeidet die Elastizität von ohv-Konstruktionen, nicht aber die seitliche Belastung der Ventile während der Öffnungsphase. Trotzdem taugte das Prinzip in den Honda-Vierzylindern für Drehzahlen bis etwa 10000/min – bei den 350er- und 400er-Motoren sogar mehr – und vorbildliche Laufleistungen. Trotz der komplizierten Bearbeitung der Nockenwelle mit je einer Ein- und Auslassnocke im Wechsel und der komplexen Kipphebelmechanik waren die ohc-Motoren offenbar günstiger zu produzieren als Triebwerke mit zwei obenliegenden Nockenwellen, sodass Honda gute zehn Jahre lang an ihnen festhielt.
dohc, Tassenstößel
Nach den exotischen MV-Vierzylindern der späten 1960er-Jahre war Kawasaki 1972 der erste Hersteller, der einen Motor mit zwei obenliegenden Nockenwellen in Großserie brachte. Geschliffene Plättchen, zunächst auf, dann zur Gewichtsersparnis unter den Tassenstößeln dienten zum Einstellen des Ventilspiels. Der oben gezeigte Motor der Suzuki RF 600 von 1993 bedeutete eigentlich einen Rückschritt in Sachen Ventilbetätigung, hatte doch die luft-/ölgekühlten Motorenbaureihe, die 1985 in der GSX-R 750 debütierte, bereits Gabelschlepphebel. Den Wechsel zum Tassenstößelmotor vollzog man aus Kostengründen, ebenso wie Honda mit der CBR 600 F vom Typ PC 25 oder Kawasaki mit der ZX-7R, um nur zwei weitere Beispiele zu nennen. Erst als die 1000er-Supersportler die 200-PS-Grenze ins Visier nahmen, kamen Schlepphebel wieder in Betracht.
dohc, Schlepphebel
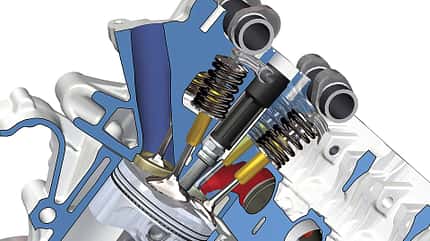
Es sind die geringeren bewegten Massen, die den größten Vorteil von Schlepphebeln gegenüber den Tassenstößeln bringen und mithin die Möglichkeit, höhere Ventilbeschleunigungen zu realisieren. Präzisierend muss man „Gleitschlepphebel“ schreiben, denn ein Rollenschlepphebel würde den Gewichtsvorteil wieder zunichtemachen. Weiterhin stützen Schlepphebel die durch das Anlaufen der Nocke entstehenden Seitenkräfte effizienter ab als Tassenstößel. Angeblich stammen Hebel des BMW S 1000 RR-Vierzylinders von den BMW-Formel-1-Motoren, die über 18.000/min drehten. Für zahmere Ausführungen des S 1000-Vierzylinders, die keine 14.000/min drehen, verzichtete man auf das Ausfräsen der Seitenflächen, um Kosten zu sparen. Als für 2015 die Neukonstruktion der YZF-R1 anstand, brachte auch Yamaha die Schlepphebeltechnik der MotoGP-Motoren in die Serie. Man darf gespannt sein, wann weitere Hersteller nachziehen werden. Die Vorteile in Sachen Leistungscharakteristik liegen auf der Hand.
Clever kombiniert: Mischformen
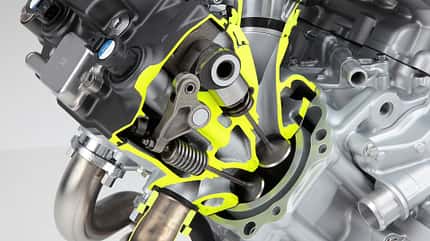
Eine desmodromische Ventilsteuerung, wie sie für Ducati-Motoren typisch ist, wäre ohne den Einsatz von Kipphebeln zum Schließen der Ventile nicht möglich. Um beim Öffnen möglichst geringe Massen zu bewegen, kombinieren die Konstrukteure Schlepp- und Kipphebel. Das Streben nach leichten und kompakten Zylinderköpfen stand bei den sogenannten Unicam-Motoren im Vordergrund, die bei Motocrossern, aber auch in den VFR 1200-Modellen eingesetzt wurden. Die Einlassventile werden über Tassenstößel betätigt, die kleineren Auslassventile von der gleichen Nockenwelle über einen Rollenkipphebel. Der erste V2 von Harley-Davidson besitzt je ein hängendes Einlass- und ein stehendes Auslassventil pro Zylinder. Entsprechend unterschiedlich werden die Ventile betätigt.
Interview
Als Hauptvorteil einer Ventilbetätigung durch Gleitschlepphebel im Vergleich zu Tassenstößeln gilt die geringere bewegte Masse. Welche anderen Vorteile haben Gleitschlepphebel?
Für BMW sind seit jeher hochdrehende Saugmotoren mit entsprechend hoher Literleistung von großer Bedeutung. Dieses Konzept bietet entscheidende Vorteile in puncto Ansprechverhalten und Gewicht. Der Ventiltrieb spielt hier, also bei der Realisierung optimaler Ladungswechsel, eine wesentliche Rolle. Um die erforderliche hohe Literleistung bei gleichzeitig gutem Drehmomentverlauf darzustellen, sind füllige Nockenprofile erforderlich. Hierfür ist der Gleitschlepphebel die optimale Konstruktion. Der größte Vorteil der Gleitschlepphebel ist das günstige Verhältnis von hoher Biegesteifigkeit und geringer bewegter Masse. Aufgrund der hohen Belastungen ist hierbei eine verschleißbeständige Oberfläche wie zum Beispiel eine DLC-(diamond-like carbon)-Beschichtung erforderlich.
Lassen sich die Vorteile der Schlepphebel bezüglich der möglichen Ventilbeschleunigungen ungefähr quantifizieren? Wie groß sind sie?
Bei heutigen Motorrädern wie der S 1000 RR mit einer Höchstdrehzahl von 14.200/min und einer Literleistung von 200 PS treten Ventilbeschleunigungen von bis zu 40.000 m/s² auf. Um die daraus resultierenden Massenkräfte zu bewältigen, ist neben dem Schlepphebel der Einsatz von ultraleichten Titanventilen notwendig. Andere Ventiltriebe liegen bezüglich der Ventilbeschleunigung je nach Bauart um Faktoren niedriger.
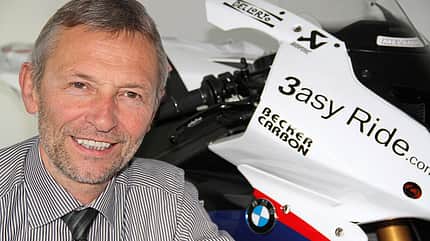
Ausgehend von einem Motorrad-Vierzylindermotor mit 1000 cm³ Hubraum und einer Bohrung von 76 bis 80 Millimetern: Bei welcher Drehzahl und Literleistung sehen die BMW-Motorentechniker die Grenze der Ventilbetätigung durch Tassenstößel?
Um den Ansprüchen von BMW in Bezug auf einen fülligen Drehmomentverlauf bei gleichzeitig hoher Literleistung gerecht zu werden, sehen wir oberhalb von etwa 10.000/min den Schlepphebel als das vorteilhaftere Konzept an. Wie andere Hersteller zeigen, sind Drehzahlen von 13.500/min und Literleistungen von etwa 200 PS auch mit Tassenstößel möglich, allerdings nur mit kleineren Ventilen und/oder weniger fülligen Nockenerhebungen. Dies führt zu einem deutlich sichtbaren Unterschied in den Leistungskurven.
Gegenüber einem Redakteurskollegen bezeichnete ein BMW-Techniker einst die Gleitschlepphebel der K 1200/1300- sowie der ersten Boxer-Baureihe mit dohc-Ventiltrieb als eine der teuersten Motorkomponenten, sowohl was die Entwicklungs- als auch was die Produktionskosten betrifft. Welche besonderen Schwierigkeiten treten bei der Entwicklung und Fertigung von Gleitschlepphebeln auf?
Als vor nunmehr knapp 20 Jahren die K 1200 S entwickelt wurde, war der Einsatz von Gleitschlepphebeln nur aus Motorsportanwendungen bekannt. Die Herausforderung lag darin, die sehr hohen Flächenpressungen zu beherrschen, die zwischen der Nocke und der Gleitfläche des Schlepphebels auftreten. Die Lösung dafür ist eine Beschichtung der Gleitfläche mit einer Oberfläche, die so hart und verschleißfest ist wie ein Diamant. Auch bekannt als DLC (diamond-like carbon). Dieses Verfahren war damals nur für Kleinstserien verfügbar und musste für Großserienstückzahl weiterentwickelt werden. Daher war sowohl die Entwicklung als auch die Industrialisierung entsprechend aufwendig und teuer. Mittlerweile entspricht es jedoch dem Stand der Technik.
Rollenschlepphebel erzeugen bei niedrigen Drehzahlen ein geringeres Schleppmoment als Gleitschlepphebel oder Tassenstößel. Welche weiteren Vorteile hat diese Art der Ventilbetätigung, und wo liegen ihre Nachteile?
Der wesentliche Vorteil des Rollenschlepphebels liegt in der geringeren Reibleistung. Der Nachteil liegt in der geringeren Steifigkeit, im Gewicht und im beanspruchten Bauraum. Damit ergeben sich geringere mögliche Ventilbeschleunigungen und Maximaldrehzahlen.
Welche Vor- und Nachteile haben Hülsen- und Zahnketten als Nockenwellenantrieb?
Die Zahnkette, welche auch als „Silentchain“ bezeichnet wird, hat ihren wesentlichen Vorteil in der Akustik und darüber hinaus bei gleicher Abmessung in einer höheren übertragbaren Kettenkraft. Der Vorteil der Hülsenkette liegt in der geringen Überspringneigung. Dadurch können die Spann- und Führungsschienen kompakter ausgeführt werden.
Ein Rückblick in die Entwicklungsgeschichte des BMW-Boxermotors: Von der R 1100 RS von 1994 bis zur ersten Generation der R 1200 GS wurden die Ventile über je eine hochgelegte Nockenwelle und je ein Paar kurzer Stoßstangen sowie Kipphebel betätigt. Als Grund wurde die geringere Baubreite im Vergleich zu einem dohc-Ventiltrieb genannt. Doch der erste dohc-Boxer geriet schmaler als sein Vorgänger. Welche Erkenntnisse beziehungsweise Fortschritte haben dies ermöglicht?
Bei der Entwicklung des dohc-Boxers stand eine Performancesteigerung des Aggregates im Vordergrund, gleichzeitig sollte die Baubreite nicht zunehmen. Durch eine Kombination des innovativen Steuertriebes mit den konisch geschliffenen Nocken und radial angeordneten Ventilen konnte eine deutliche Verbesserung des Ladungswechsels und der Drehzahlfestigkeit erreicht werden. Die neue Brennraumgeometrie mit geänderter Lage und Größe der Kalotte tragen ebenso nicht nur zur Verbesserung des Ladungswechsels, sondern auch zur Kompaktheit und damit zur minimalen Baubreitenänderung bei.