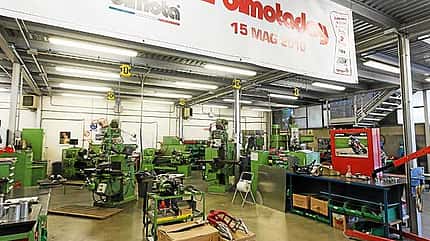
Bevor Ignazio Fancello darangeht, eine Serie von Bimotas zu montieren, ist er erst einmal weg. Er geht Teile sammeln. Nach und nach füllt er die Regale und Tische im ersten Stock des kleinen Fabrikgebäudes in der Via Giaccaglia 38 in Rimini mit Verkleidungen, Kotflügeln, Bremszangen und Leitungen. An der Decke hängen Schwingen, Schrauben, Muttern und Scheiben aller benötigten Arten schüttet er in die Sortierkästen einer Regalwand auf Rollen.Dann holt er den Motor.
Gleich nebenan liegen die frisch angelieferten Ducati-Triebwerke in Transportgestellen nebeneinander; auf einem kleinen Hubwagen werden sie zu einem der fünf Montageständer im Produktionsbereich gerollt, dann hängt Ignazio einen Motor an einen kleinen Kran, hebt ihn hoch und setzt ihn auf den Ständer. Dieses Mal ist es ein luftgekühlter Zweiventiler, bestimmt für die erste von 25 Tesi 3D. Das ist die normale Losgröße bei Bimota. Die rot lackierten, an einem Deckenträger hängenden Hinterradschwingen der db7 und der Tesi stechen Besuchern als Erstes ins Auge. Stolz zeigt Entwicklungschef Massimo Gustato die Bremszangen, die Grimeca eigens für die Tesi mit Bimota-Schriftzug anfertigt."Brembo wollte das nicht, die machen das nicht einmal für große Hersteller, glaube ich, und für uns schon gar nicht."
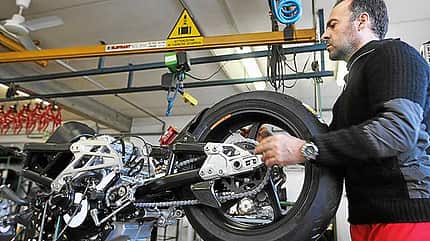
Die Tesi-Kleinserie, die Ignazio eben gestartet hat, löst eine Reihe von db8 ab, die nebenan, auf Montageständern oder schon auf den eigenen Rädern stehend, ihre Vollendung erwarten. „Moto da completare“, Motorrad zum Vervollständigen, verkündet ein angehängter Laufzettel in Klarsichthülle. Auf einem Rollwagen sind bereits die omegaförmigen, aus dem Vollen gefrästen Aluteile angerichtet, die - mit dem Motor verschraubt - den Kern des einzigartigen Fahrwerks mit Achsschenkellenkung bilden. Für das Festziehen der langen Bolzen benutzt Ignazio keinen Druckluftschrauber; das erledigt er konventionell und sorgfältig mit einem Drehmomentschlüssel. Er kann sich Zeit nehmen. Die Produktion ist bei Bimota nicht in einzelne Arbeitsschritte aufgeteilt, die dann jeder für sich optimiert werden. Hier gilt der Grundsatz: Ein Mann baut ein Motorrad. Es gibt Pläne, die Motorräder in Zukunft mit dem Namen ihres Monteurs zu versehen.
Der zweite Grund dafür, dass Ignazio sich Zeit nehmen kann, ist weniger erfreulich als die Tatsache, dass die kleine Motorradmanufaktur bei der Produktion auf die Arbeit von hochqualifizierten Mechanikern setzt: Die Verkäufe sind in der Krise drastisch eingebrochen. "2008 haben wir 400 Motorräder gebaut und verkauft, 2010 werden es höchstens 200 sein. Ich wäre froh, wenn wir diese Zahl bis zum Jahresende erreichen würden; momentan (9. Dezember 2010, Red.) stehen wir bei 180. Es ist ein schwarzes Jahr", sagt Massimo. Das ist auch der Grund dafür, dass Ignazio heute alleine arbeitet. In Hochzeiten schrauben noch zwei Kollegen mit ihm die exklusiven Bimotas zusammen, drei weitere kümmern sich um die Vormontage einzelner Baugruppen, ziehen beispielsweise die Reifen auf die neu eingeführten OZ-Räder und versehen diese mit Bremsscheiben. Die im Herbst 2010 vorgestellte, vergleichsweise günstige db8 mit Ducati-1198-Motor, dem gleichen Fahrwerk wie die db7, aber einfacherer GFK- statt Kohlefaserverkleidung soll die Absatzzahlen wieder nach oben ziehen.
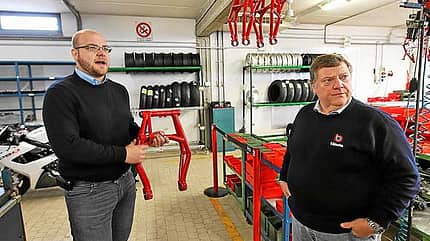
Vielleicht lässt Ignazio deshalb die eben erst auf Kiel gelegte Tesi stehen und wendet sich einer halbfertigen db8 zu. Wahrscheinlicher ist jedoch, dass er die hochkomplexe Mechanik der Di-Fazio-Vorderradnabe nicht unter Beobachtung durch den MOTORRAD-Fotograf und -Redakteur, sondern in Ruhe montieren und einstellen will. Dagegen sind der Einbau des Hinterrads und die Justage von Spur und Kettendurchhang an der db8 reine Routine. Auch die Montage der Drosselklappenkörper mitsamt Luftfilter und Airbox, die er danach in Angriff nimmt, geht ruckzuck. Kurz und kräftig gedrückt, ploppen die Anschlussstücke in ihre zart gefetteten Gummistutzen, rasch sind die Schellen festgezogen. Jeder abgeschlossene Arbeitsschritt wird getreulich in einen Laufzettel eingetragen.
Airbox und Auspuff der db7-/db8-Modelle, und deshalb auch die Software der Einspritzung, hat Bimota in Zusammenarbeit mit der Firma Walbro selbst entwickelt. Der Ducati-Motor ist durch die geänderte Abstimmung besser fahrbar geworden, vollzieht etwas weicher und benimmt sich beim Beschleunigen weniger aggressiv. Nicht nur für die Landstraße eine angenehme Charakteristik, sondern auch für die Rennstrecke, wie der Autor bei einem früheren Termin feststellen konnte und MOTORRAD-Tests bestätigt haben.
Als Kleinsthersteller mit minimalem Entwicklungsbudget konnte und kann es sich Bimota nicht leisten, einen eigenen Motor zu entwickeln, geschweige denn zu fertigen. Der Versuch, den 500er-Zweizylinder-Zweitakter mit Direkteinspritzung als Antrieb der Vdue zur Serienreife zu bringen, führte in den Konkurs. Zumal die gleichzeitige Steigerung der Produktion auf bis
zu 900 Motorräder im Jahr nicht die erhoffte Kapitaldecke schuf, sondern massive Qualitätsprobleme mit sich brachte. Heute betätigt man sich in bester Firmentradition wieder hauptsächlich als Fahrwerks- und Designentwickler und lässt die maximale Produktionskapazität bei etwa 600 Einheiten pro Jahr. Davon abgesehen, dass eine Erhöhung momentan sinnlos wäre, würde sie selbst in Zeiten guter Konjunktur eine unverhältnismäßig hohe Investition voraussetzen. Wie nicht nur die eigene Firmenhistorie gezeigt hat.
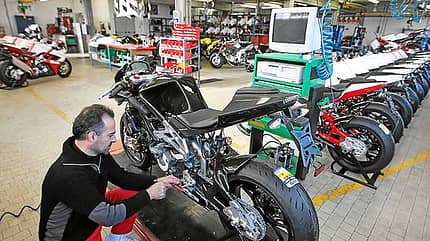
Das Bimota-Engagement in der Moto2-Klasse, wo verschiedene Fahrwerkshersteller mit Honda-Einheitsmotoren antreten, ist daher nicht als Abenteuer zu verstehen, sondern als Investition mit dem Ziel, den einen oder anderen Auftrag für den Bau eines Chassis zu erhalten. Doch abgesehen von drei Fahrwerkskits, die der deutsche Motorradhändler Denis Hertrampf bestellt hat, um superedle Rennstreckenmotorräder für betuchte Sammler aufzubauen, hat sich diese Hoffnung noch nicht erfüllt.Auf den Maschinen im Erdgeschoss wurden früher die Dreh- und Frästeile gefertigt, für deren Finish Bimota berühmt ist. Heute entstehen dort nurmehr Teile für Rennmaschinen oder Prototypen. Sie werden im Straßenbetrieb und nebenan auf Belastungsprüfständen getestet. Wenn die endgültige Ausführung feststeht, bestellt Bimota die Serienteile bei einem Spezialbetrieb. Das gleiche gilt für die Stahl-Gitterrohrsegmente der Rahmen, die bei Verlicchi geschweißt werden, und die Verkleidungsteile.
Bimota ist also heute ein reiner Entwicklungs- und Montagebetrieb.Impulse setzen möchte der traditionell innovative Kleinhersteller bei der Verwendung von Karbon für tragende Teile. Davon zeugt die db7 oronero, deren Rahmen dort, wo die Standardausführung ein stählernes Rohrgeflecht trägt, mit sorgfältig gewickelten und verklebten Karbonröhren rund acht Kilogramm Gewicht einspart. Ob das hält? "Natürlich, im Rennstreckenbetrieb haben wir sogar schon Rahmen getestet, deren Karbonsegment noch um die Hälfte leichter war", sagt Chefentwickler Massimo. "Ohne Probleme. Aber für den normalen Betrieb bauen wir Reserven ein."
Und wie viele Leute sind "wir"? "Derzeit 25. Neben den sechs Leuten in der Produktion noch zwei Entwickler und ein Designer, ein Frässpezialist, drei Leute für Vertrieb, Ersatzteilwesen und Garantieabwicklung. Und dann haben wir momentan noch drei freie Mitarbeiter für ein spezielles Projekt." Leider war beim Besuch von MOTORRAD keine Spur davon zu entdecken.
Kreativ, exklusiv, teuer

Hätte Massimo Tamburinis Honda CB 750 beim Fahren auf dem GP-Kurs von Misano nicht so erbärmlich gewackelt, hätte es Bimota wohl nie gegeben. So aber entstand neben einem tauglichen Fahrwerk für die Honda die Idee, eine Motorrad-Manufaktur zu gründen, welche die unterschiedlichsten Motoren in hochwertige Fahrwerke und aufregende Designs packte. 1973 war es soweit; die Anfangssilben der Gründernamen Bianchi, Morri und Tamburini bildeten den Firmennamen. Die bis heute erfolgreichste Bimota-Konstruktion, die bahnbrechende YB4 mit einem der ersten Alu-Brückenrahmen im Motorradbau, entstand 1988. Stets blieben die Stückzahlen gering und die Preise hoch; der Versuch zu expandieren, um die Entwicklungskosten für einen revolutionären Zweitakter aufzubringen, führte im Jahr 2000 in die Pleite. 2003 erweckten neue Investoren die Firma wieder zum Leben, heute baut sie ausschließlich Motorräder mit luft- und wassergekühlten Motoren von Ducati.