Oberflächenbeschichtungen - nichts anderes sind Lack oder ein galvanischer Auftrag - müssen zwei Aufgaben erfüllen. Zum einem sollen sie das Bauteil vor Korrosion schützen, zum anderen eine ansehnliche Oberfläche erzeugen. Natürlich soll das Ganze auch möglichst lange halten - doch hier fangen die Probleme schon an.
So können Lacke auf dynamisch oder statisch hoch beanspruchten Teilen wie Stoßdämpferfedern, Felgen, Fahrwerkskomponenten oder Rahmen bereits nach wenigen Monaten alt aussehen, da sie nach dem Aushärten früher oder später spröde werden. Folge: Der teuer und mühsam aufgebrachte Lack nimmt durch Steinschlag oder Witterungseinflüsse Schaden. Was mit kleinen Abplatzern beginnt, führt über kurz oder lang zur Korrosion des darunter liegenden Metalls. Dann muss erneut lackiert werden.
Gefügeveränderung beim Verchromen
Galvanische Beschichtungen, landläufig auch als Verchromen bekannt, sind da schon dauerhafter und halten meist viele Jahre. Doch sie haben einen entscheidenden Nachteil. Speziell Teile, die hoch mechanisch belastet sind, dürfen galvanisch nicht behandelt werden, weil sie durch die Oberflächenbehandlung (Polieren) und durch die aufgebrachte galvanische Schicht ein verändertes Zug- und Bruchverhalten gegenüber dem unbehandelten Teil aufweisen. Der Materialexperte spricht hier von einer Gefügeveränderung. Die meisten Prüforganisationen lehnen daher galvanisch überarbeitete Komponenten im Fahrwerks- oder Bremsenbereich kategorisch ab, verweigern die Zulassung oder das Prüfsiegel.
Spätestens an diesem Punkt fangen viele an zu überlegen, ob es nicht Alternativen gibt, Oberflächen dauerhaft zu versiegeln oder zu verschönern. Die Lösung, die hier immer öfter genannt wird, ist Pulverbeschichten. Obwohl diese Methode seit vielen Jahren erfolgreich in der Industrie in verschiedensten Bereichen angewendet wird und sich dort auch bestens bewährt hat, lehnen sie viele Besitzer klassischer Motorräder strikt ab. Als Begründungen werden hier meist das Kunststoffartige Finish der Oberflächen und die eingeschränkte Farbauswahl genannt. Weil das Pulverbeschichten zu den dauerhaftesten Oberflächenvergütungen gehört, hat MOTORRAD Classic bei einem bekannten Pulverbeschichter aus Geretsried, 40 Kilometer südlich von München, nachgefragt, welche Möglichkeiten sich heute für Restaurierer von klassischen Motorrädern mit diesem Verfahren eröffnen.
Überholtes Vorurteil
Gleich zu Beginn räumt Josip Barbir, der Inhaber einer Firma für Pulverbeschichtungen, erst einmal mit einem sich hartnäckig haltenden Gerücht auf: „Das Vorurteil, Pulverbeschichtungen sähen aus wie Plastik oder Kunststoffüberzüge, ist längst überholt. Das Finish der Beschichtungen gleicht einer sehr guten Lackierung. Dabei sind sowohl matte als auch glänzende Oberflächen möglich. Auch bieten die Hersteller der Pulverlacke heute die gesamte Palette der RAL-Farbtöne an. Selbst Metallic-Effekte oder Hammerschlag sind bei fein oder grob strukturierten Oberflächen möglich. Einzig Zwischen-Farbtöne, also solche, die zwischen den RAL-Farbtönen liegen, sind derzeit mit Pulverlacken nicht umsetzbar.“ Doch hieran wird gearbeitet. In den nächsten Jahren könnten mischfähige Pulverlacke erhältlich sein.
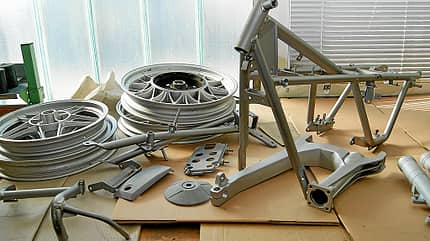
Und noch eine Einschränkung muss derzeit beim Pulverbeschichten beachtet werden. Im Gegensatz zum Lackieren können nämlich nur elektrisch leitfähige Werkstoffe pulverbeschichtet werden, die temperaturbeständig sind. Und das sind in der Regel eben solche aus Metallen. Doch auch in diesem Punkt zeichnet sich eine Lösung ab. Schon bald sollen selbst weniger temperaturbeständige Kunststoffe pulverbeschichtet werden können.
Gründliche Vorbereitung beim Pulvern entscheidend
Kommen wir zur Vorbereitung. In diesem Punkt ist die Vorgehensweise ähnlich der beim Lackieren. Hier wie dort muss das Werkstück zuerst von seinem alten Lack oder seiner alten Beschichtung befreit werden. Dies geschieht meist durch Abbeizen. Anschließend werden noch die letzten Farbreste und eventuell vorhanden Korrosion durch Sandstrahlen entfernt. Danach erfolgt das sogenannte Phosphatieren, bei dem das Werkstück entweder in ein Metallphosphatbad getaucht oder mit Metallphosphatlösung besprüht wird. Dadurch bildet sich auf der Oberfläche eine ca. sieben bis 15 µm dünne Metallphosphatschicht, die sich mit dem Grundwerkstoff fest verbindet. Je nach Verfahren handelt es sich hierbei um eine Eisen-, Mangan-, Nickel- oder Zinkphosphatschicht. Die so entstandene Metallphosphatschicht dient dem Pulverlack als Haftgrund und verhindert zuverlässig ein Unterrosten der Beschichtung. Wird die Korrosion nur mit Sandstrahlen entfernt, muss das Werkstück anschließend noch gründlich gereinigt und gegebenenfalls gut entfettet werden.
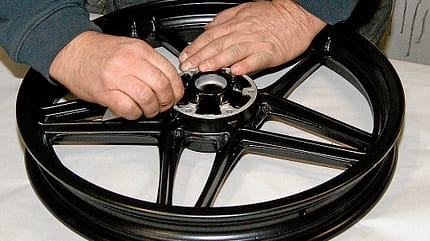
Für einen dauerhaften Schutz vor Rost muss auf die gestrahlten Teile noch vor der eigentlichen Farbpulverbeschichtung ein spezieller Pulverlackhaftgrund aufgetragen werden. Das Aufbringen des Haftgrundes geschieht auf die gleiche Weise wie das eigentliche Beschichten mit dem Farbpulver. Damit das Pulver überhaupt am Werkstück haftet, bedient man sich eines simplen, aber sehr wirkungsvollen Tricks, der zudem erklärt, warum bislang nur Teile aus Metall beschichtet werden können. Voraussetzung hierfür ist nämlich die Strom-Leitfähigkeit des Werkstückes, damit es im Pulverlackierstand elektrisch geerdet werden kann.
In der Druckluft-Pulversprühpistole wird das Pulver dagegen elektrostatisch geladen. So bildet sich ein elektrisches Feld von rund 100 Kilovolt. Resultat: Die positiv geladenen Pulverteilchen werden vom negativ geladenen Werkstück angezogen und bleiben daran haften. Gleichzeitig wird überschüssiges Farbpulver (Overspray) im Lackierstand abgesaugt. Am Werkstück selbst bleibt nur eine sehr gleichmäßige Pulverschicht zurück. Anschließend wird das bepulverte Teil vorsichtig in eine Einbrennkammer gehängt. Dort vernetzt sich das Pulver bei Temperaturen zwischen 150 bis 200 Grad Celsius zu einer homogenen Kunststoffschicht und bildet in rund 20 Minuten eine glatte Oberfläche aus. Nach dem Abkühlen können die Teile dann ohne weiteren Trocknungsprozess oder Nachbehandlung sofort eingebaut werden.
Spachtel und Füller sind tabu
Und noch etwas unterscheidet Pulverbeschichten von Lackieren. Zur Oberflächenbearbeitung können keine Füller oder Spachtel verwendet werden - sie würden beim Einbrennvorgang schlicht und einfach verbrennen. Sofern sich die Metallüberflächen vor der Beschichtung nicht in einem einwandfreien Zustand befinden, müssen sie zuvor mühsam geglättet oder verzinnt werden. Nach Ansicht von Josip Barbir lassen sich kleine Unebenheiten oder Kratzer jedoch durch mehrfaches Beschichten oder durch den Auftrag einer abschließenden Klarlack-Pulverbeschichtung ebenfalls ganz gut kaschieren.
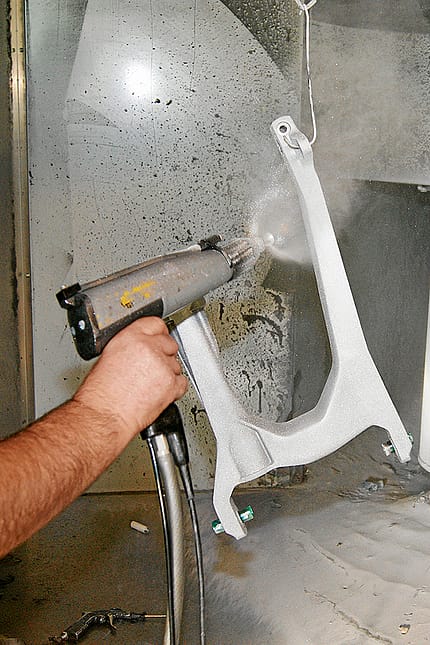
Zu den vorbereitenden Arbeiten gehört weiterhin das sorgfältige Abkleben oder Verschließen von Gewindebohrungen, Passungen und Masseanschlüssen. Wird das versäumt, muss hinterher die Beschichtung mit einem hohen mechanischen Aufwand entfernt werden. „Das Abkleben und Abdecken müssen wir bei uns selbst vornehmen“, erklärt Josip Barbir, „hierzu braucht man spezielle, temperaturbeständige Klebebänder und Verschlusskappen. Falls uns Kunden ihre Teile mit der Post schicken, empfehlen wir, alle Flächen und Gewinde, die nicht beschichtet werden dürfen, exakt zu kennzeichnen und mit uns abzusprechen.“ Dabei spielt die Größe oder die Menge der angelieferten Teile übrigens keine Rolle. Auch Kleinaufträge nehmen Pulverbeschichter wie Josip Barbir an. Ein Vorteil, den vor allem Hobbyschrauber zu schätzen wissen, die nur wenige Teile beschichten lassen wollen.
Selbst wenn im Einzelfall eine Pulverbeschichtung im Vergleich zum Lackieren einen gewissen Mehraufwand beim Vorbereiten erfordert, lohnt sich dieses Verfahren. Denn gegenüber konventionellen Lackierungen verbessert eine Pulverbeschichtung merklich die Oberflächeneigenschaften des behandelten Werkstoffes, ohne dabei eine dickere Schicht als ein herkömmlicher Lack auszubilden. Die Flächen sind dauerhaft vor Korrosion geschützt (Korrosionsschutz bis zur Korrosionsklasse C5), kratzfest, hoch schlagfest, chemikalienbeständig, witterungs- und abriebfest. Ein weiterer Pluspunkt: Die Pulverbeschichtung ist flexibel. Deshalb können mit dieser Methode zum Beispiel auch Stoßdämpferfedern vor Korrosion geschützt werden.
Sogar für hoch wärmebelastete Teile wie Auspuffanlagen oder Motorkomponenten gibt es mittlerweile temperaturbeständige Pulverbeschichtungen. Diese basieren auf Silikonharz, halten Temperaturen bis 550 Grad Celsius stand, ohne dass es zu Vergilbungen kommt. Allerdings gibt es bislang nur die Farbtöne Silber, Grau und Schwarz als Strukturlack oder seidenglänzend. Wer hingegen Teile beschichten lassen möchte, die nicht heißer als 315 Grad Celsius werden, der kann sich bedenkenlos aus der breiten Palette an RAL-Farbtönen bedienen.
Obwohl Pulverbeschichtungen in der Regel sehr viel länger halten als Lackierungen, werden auch diese nach vielen Jahren irgendwann einmal unansehnlich. Dann zeigt sich ein weiterer Vorteil dieser zweiten Haut, denn die muss nicht mit viel Mühe von Hand oder maschinell abgeschliffen werden. Das Entfernen des alten, angegriffenen Oberflächenschutzes übernehmen spezielle Lösungen. Innerhalb weniger Stunden weichen sie die Beschichtung so stark auf, dass sie problemlos und ohne Beschädigung des Werkstücks mit einem Plastikspachtel abgezogen werden können.
Die Vor- und Nachteile des Pulverbeschichtens liegen somit auf der Hand. Diese Methode bietet sich nicht nur für Fahrwerks-, Rahmen- und diverse Motorteile an, sondern auch für Kleinteile wie Griffe, Verblendungen oder Halter. Soll hier eine dauerhafte, mechanisch hoch belastbare Oberflächenversiegelung erreicht werden, ist das Pulverbeschichten eine empfehlenswerte Alternative.